Welcome to FiberGlassics®
In July 1998 this site began an attempt to recognize the style and creativity of the original fiberglass boat designs from the 50's & 60's, plus capture the spirit of a time that has since past. This site honors the pioneering minds that conceived and created these beautiful, never to be made again, classic fiberglass boats.
Within this site, you will find information on classic fiberglass boats. There are many sections. All libraries, pictures and information are FREE. Enjoy your time here.
Fiberglass Repair
by Glass Clown Boats
This is an old hole for a fuel fill. In the prep for paint, the owner asked us to make it disappear. This pictorial shows the process from start to finish.
1. Measure the thickness of the fiberglass. In this case, it's 1/8" thick.
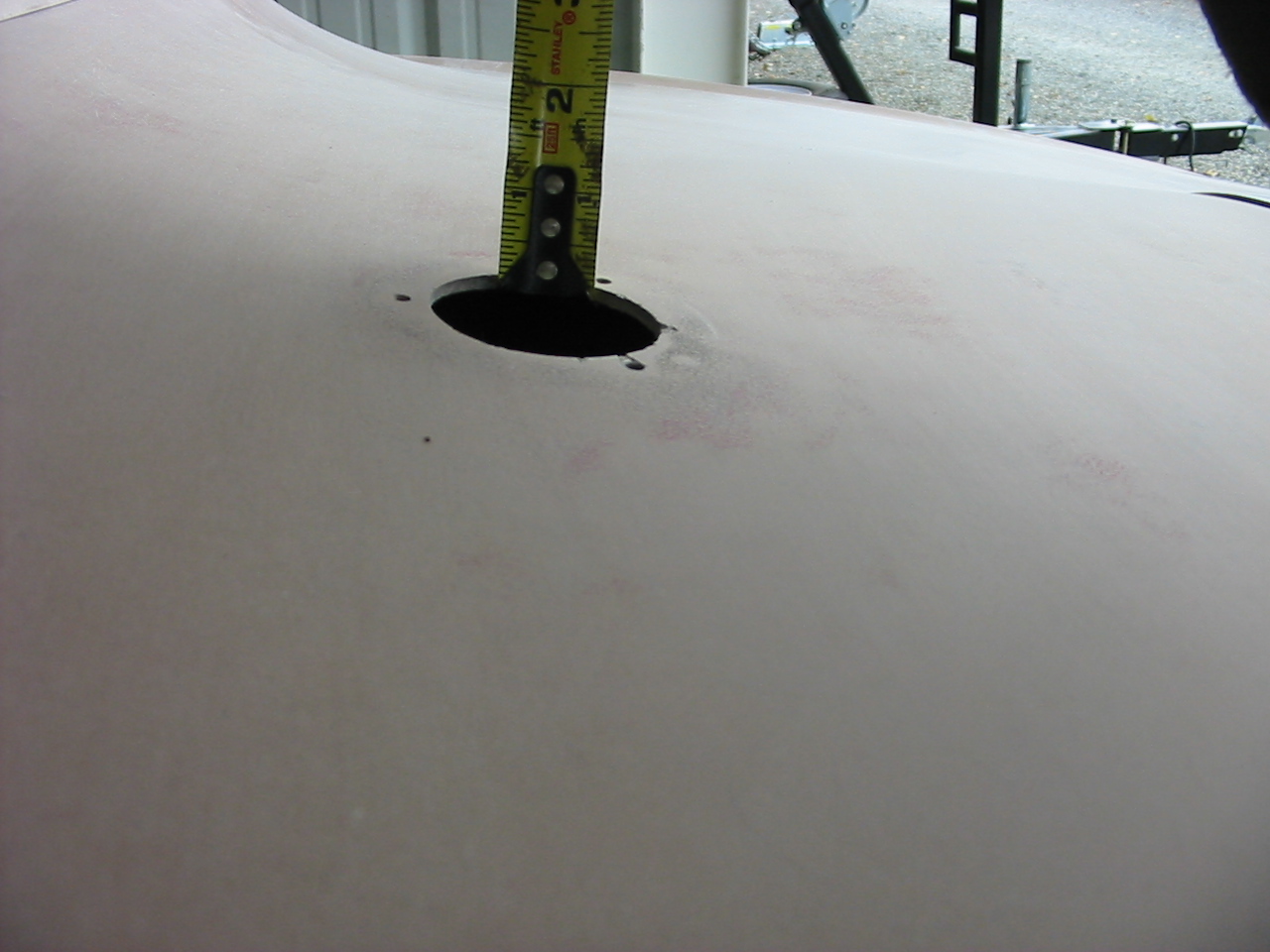
2. Then multiply that number by 10. (1/8" x 10 = 10/8" or 1-1/4")
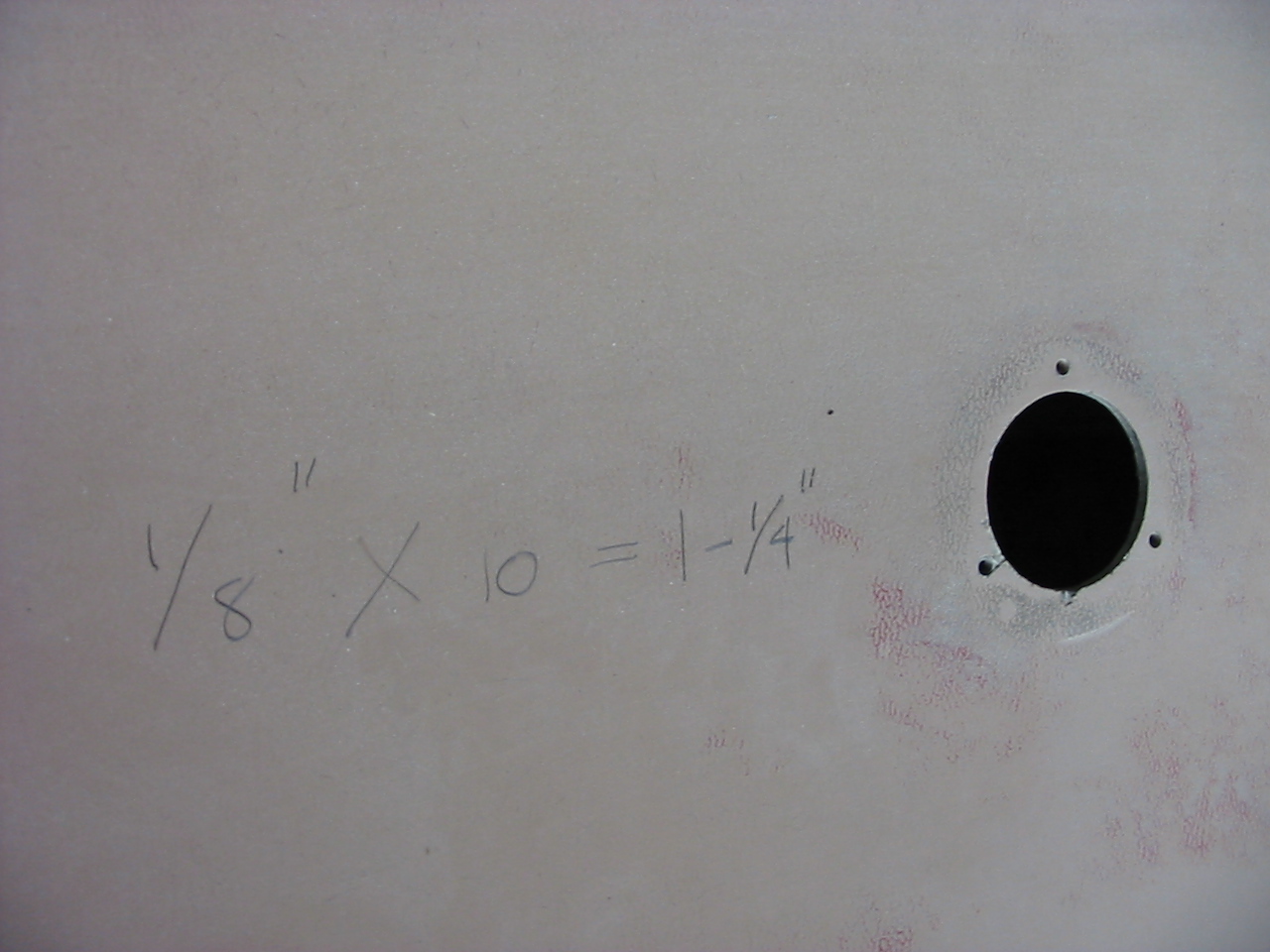
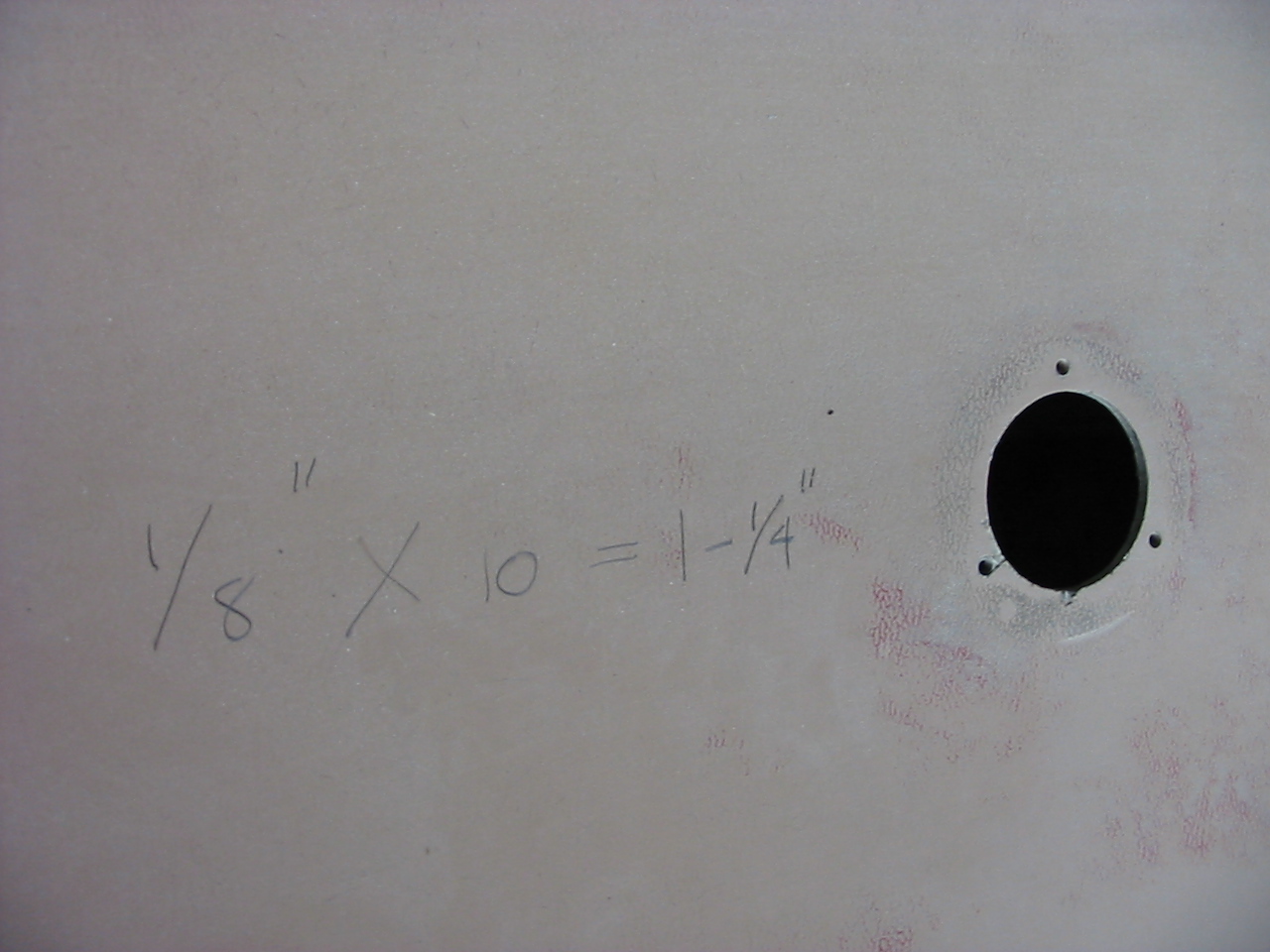
3. Now mark that distance around the perimeter of of the repair area.
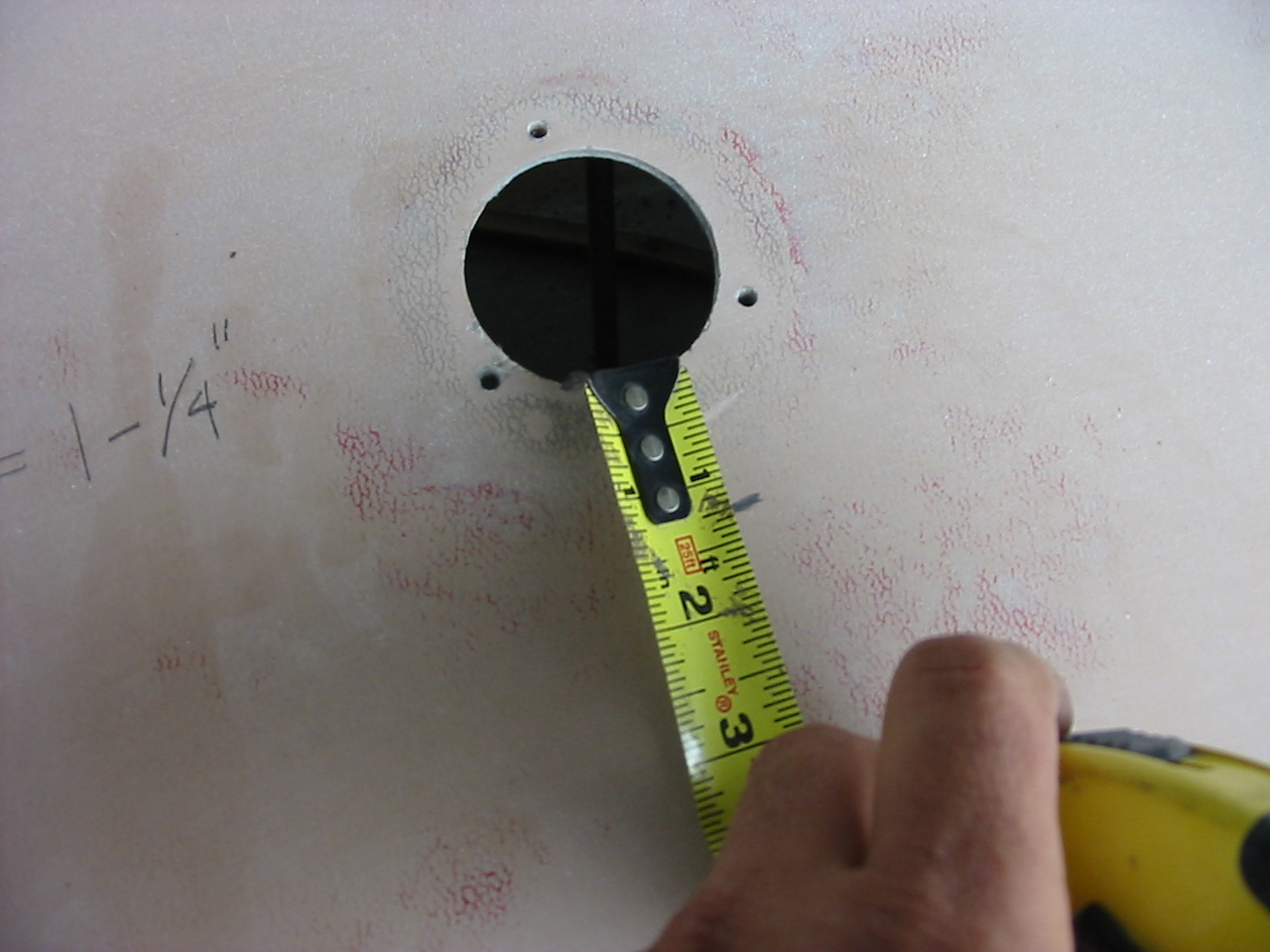
4. Connecting the hash marks
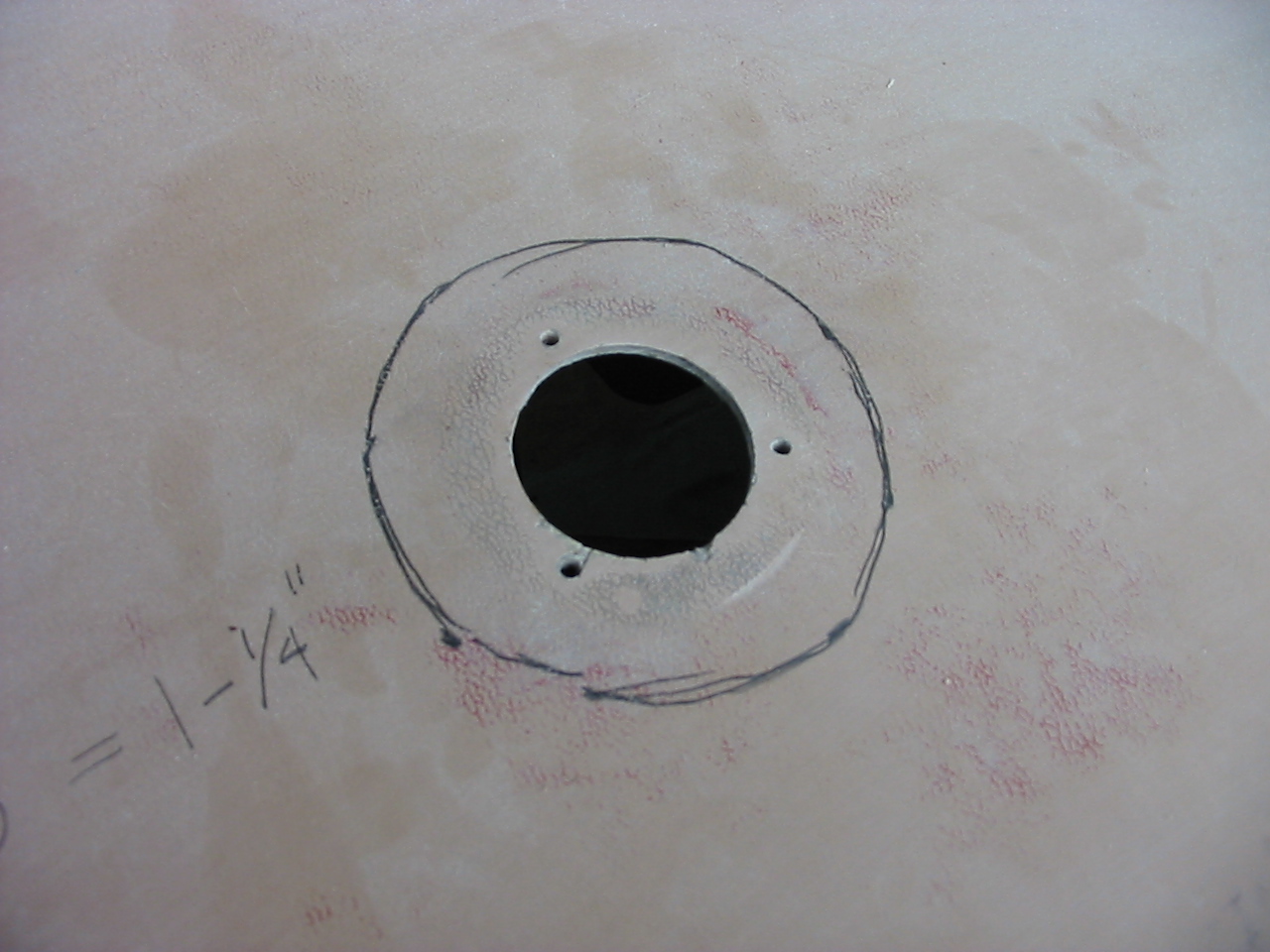
5. A grinder with an 80 grit flap wheel will give me a nice smooth taper
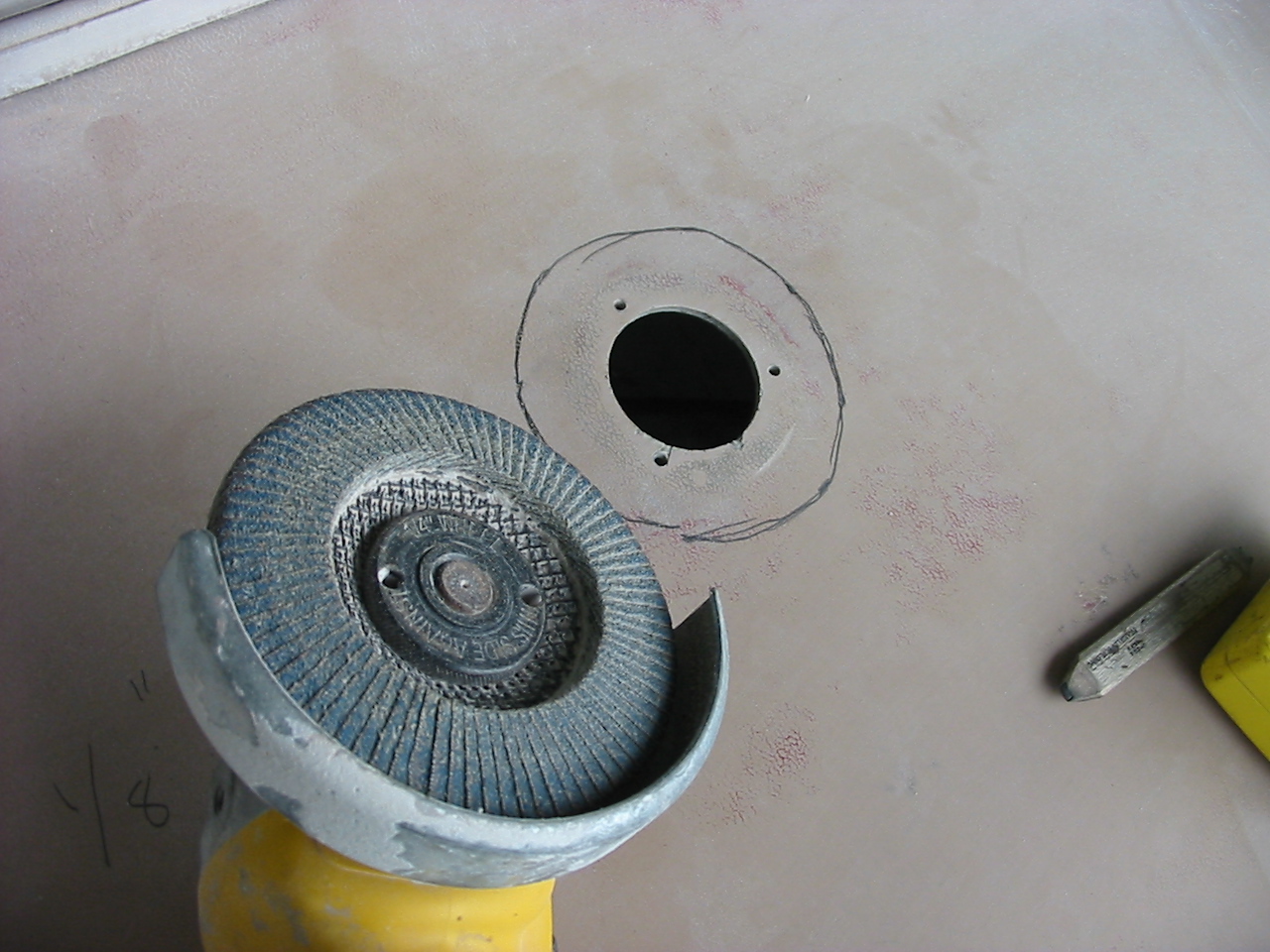
6. As always, protect yourself (safety glasses too)
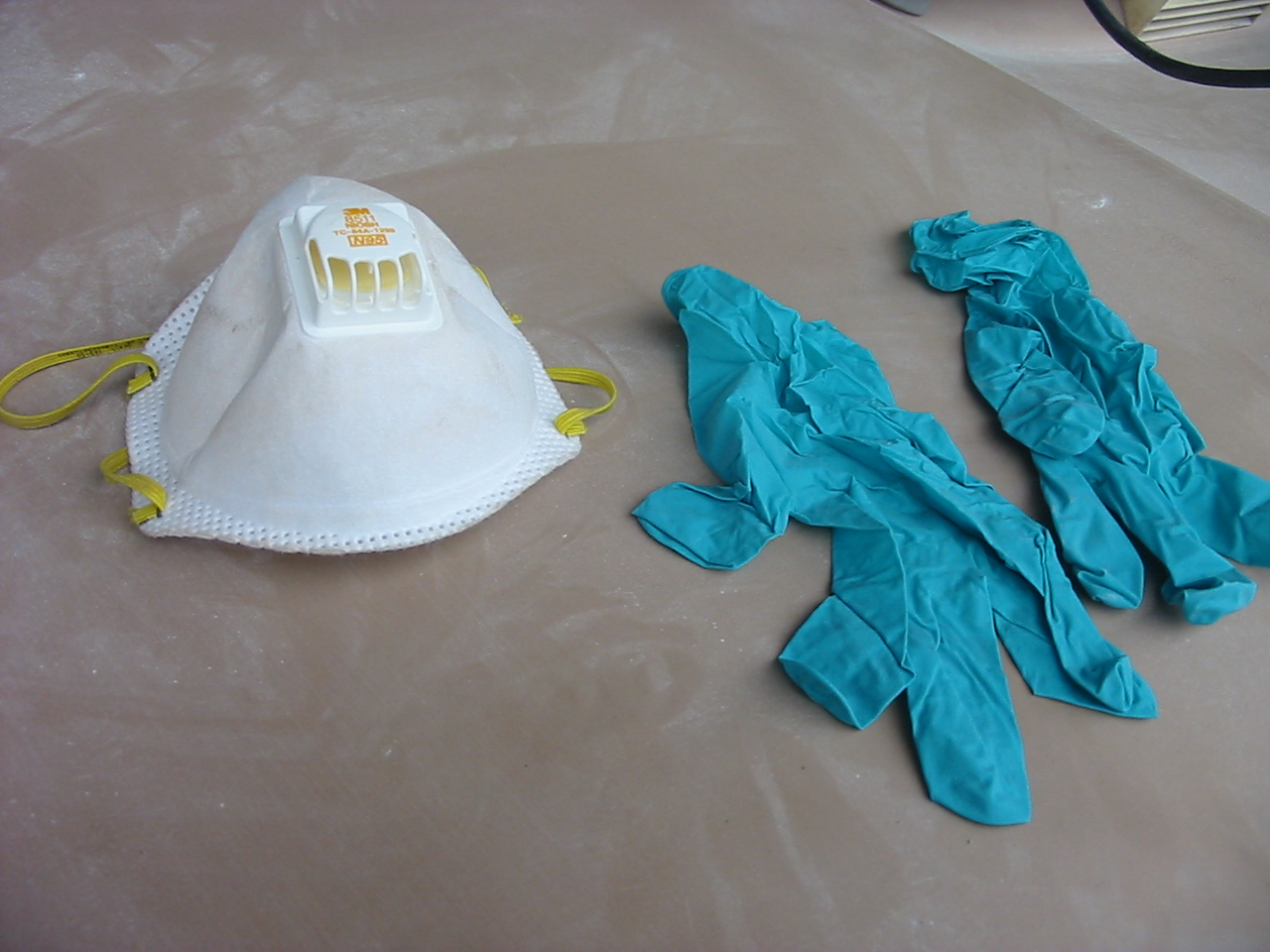
7. The repair area tapered back at a 10:1 ratio
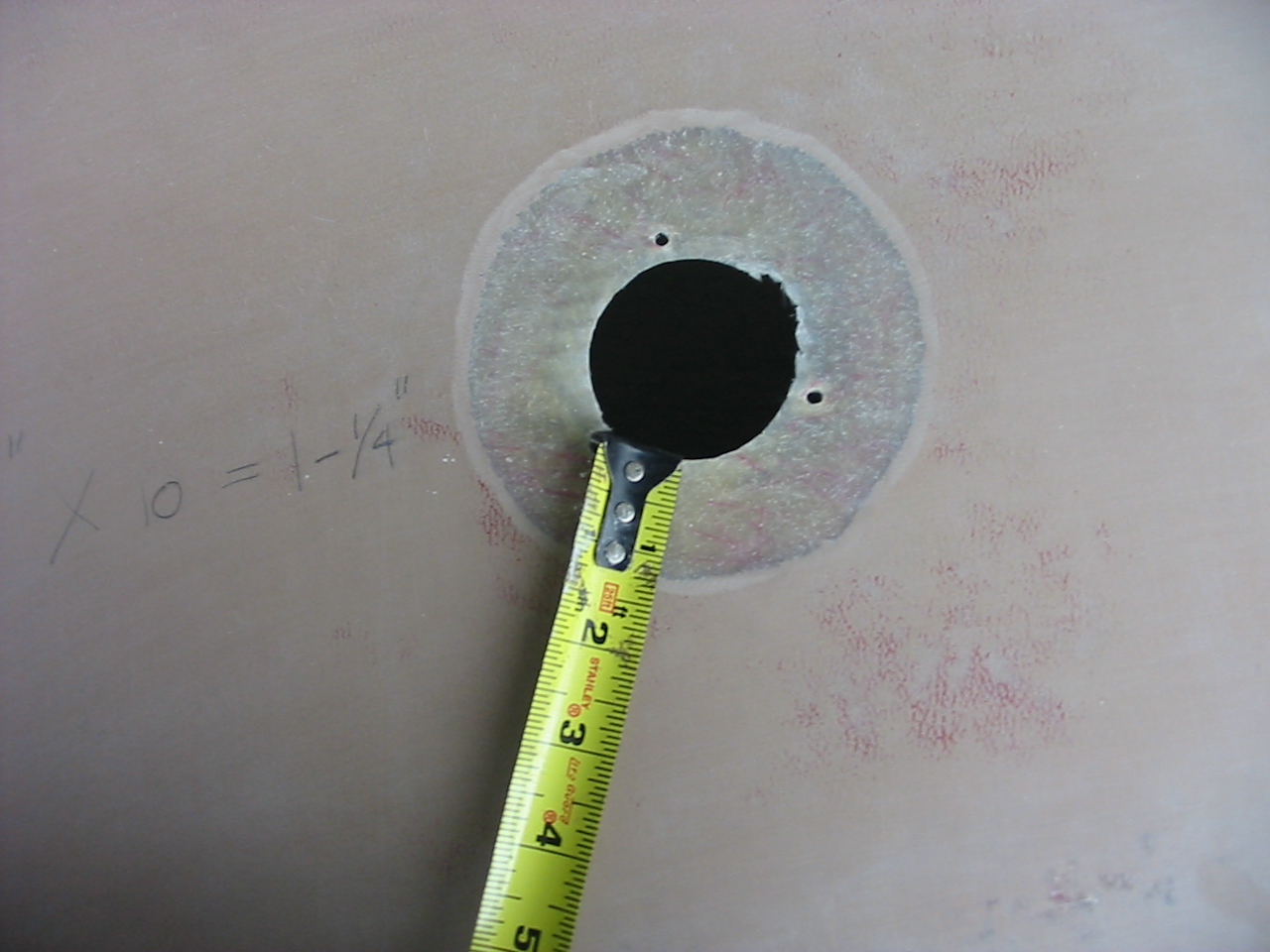
8. Which makes the total repair 4-1/2" in diameter
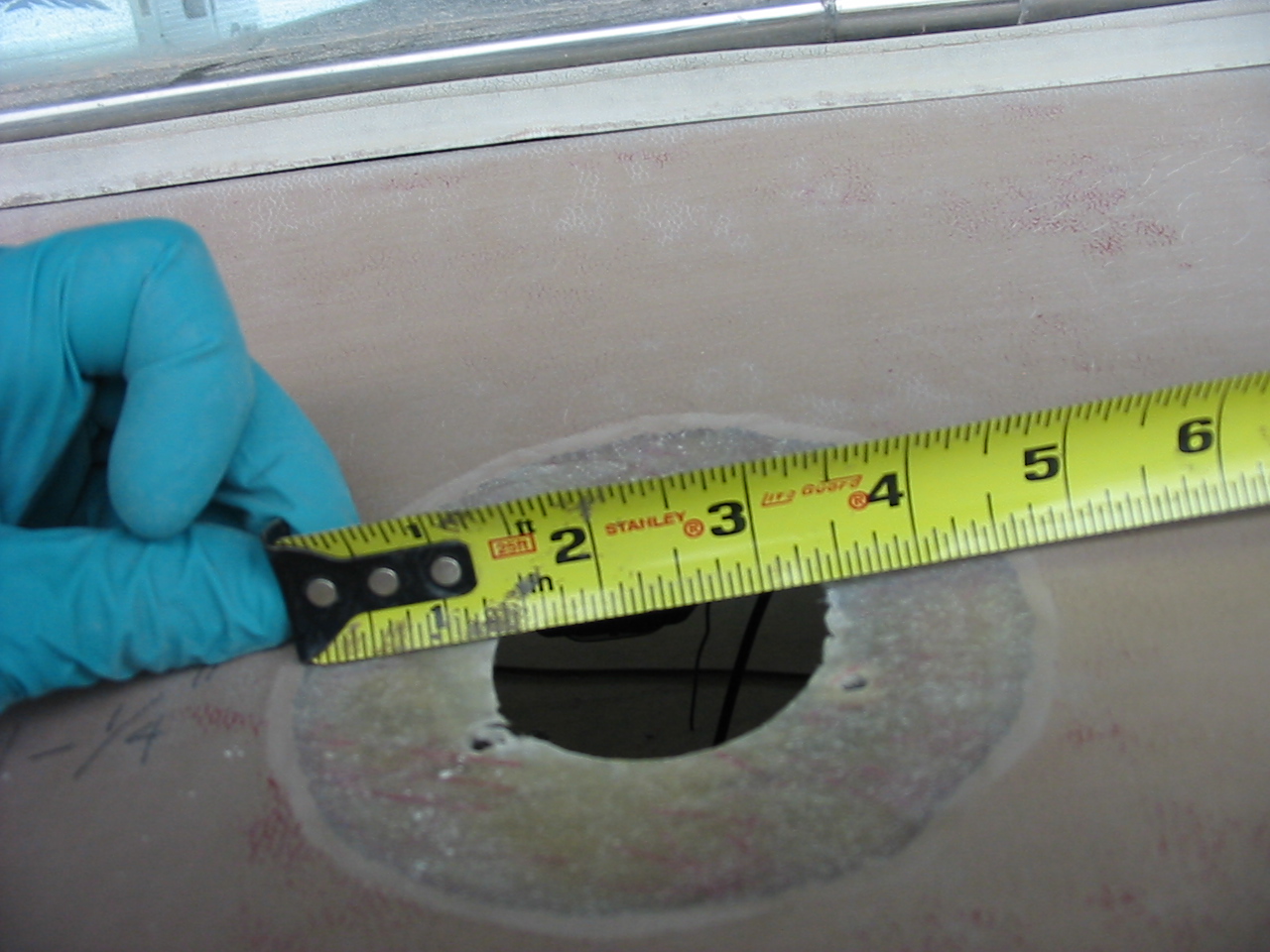
9. Each layer of fiberglass should extend 1/4" beyond the previous layer
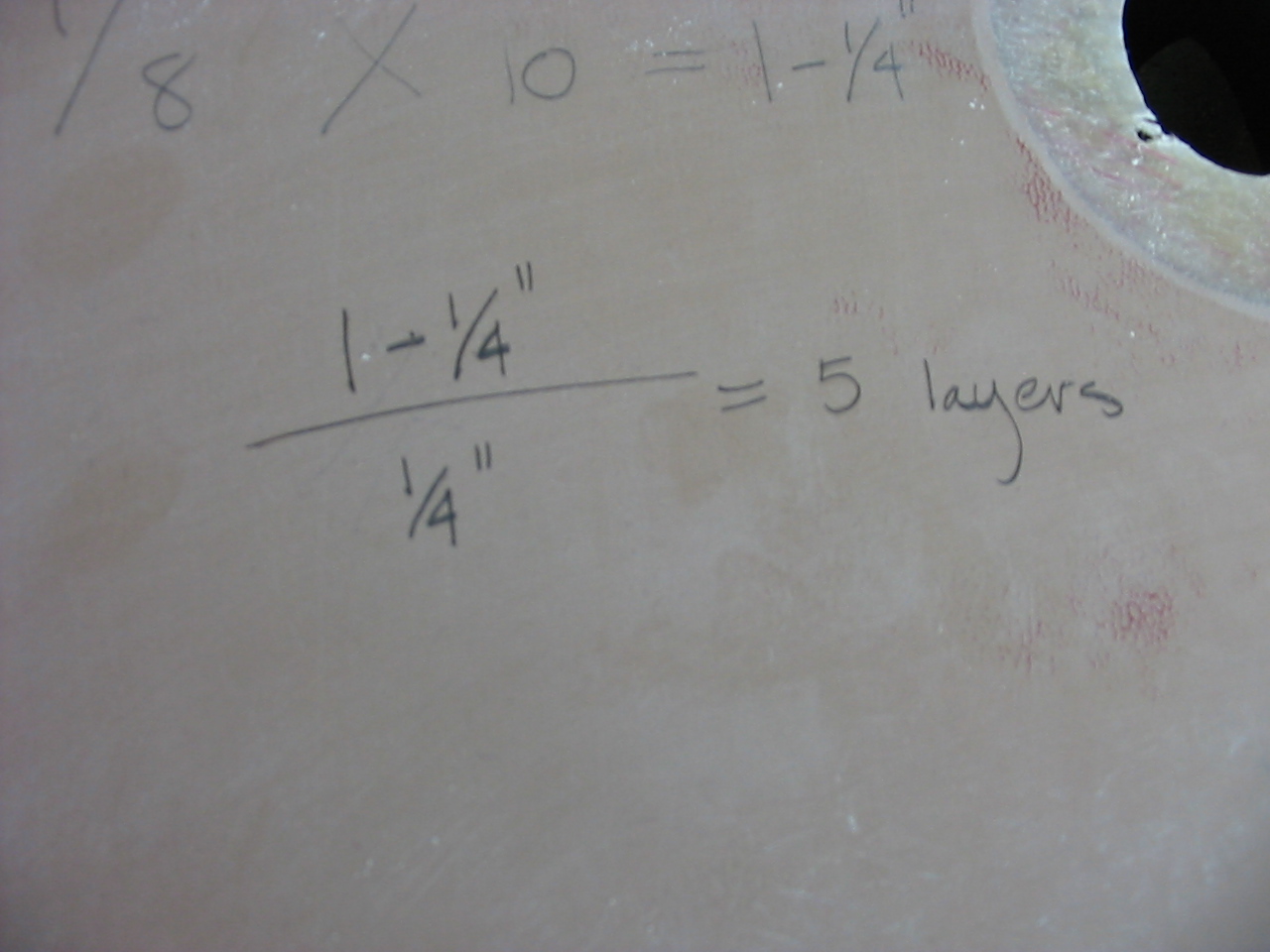
10. My fiberglass lay up schedule. Always alternate with layers of mat. Always finish with a layer of mat.

11. The fiberglass cut to a measured square.
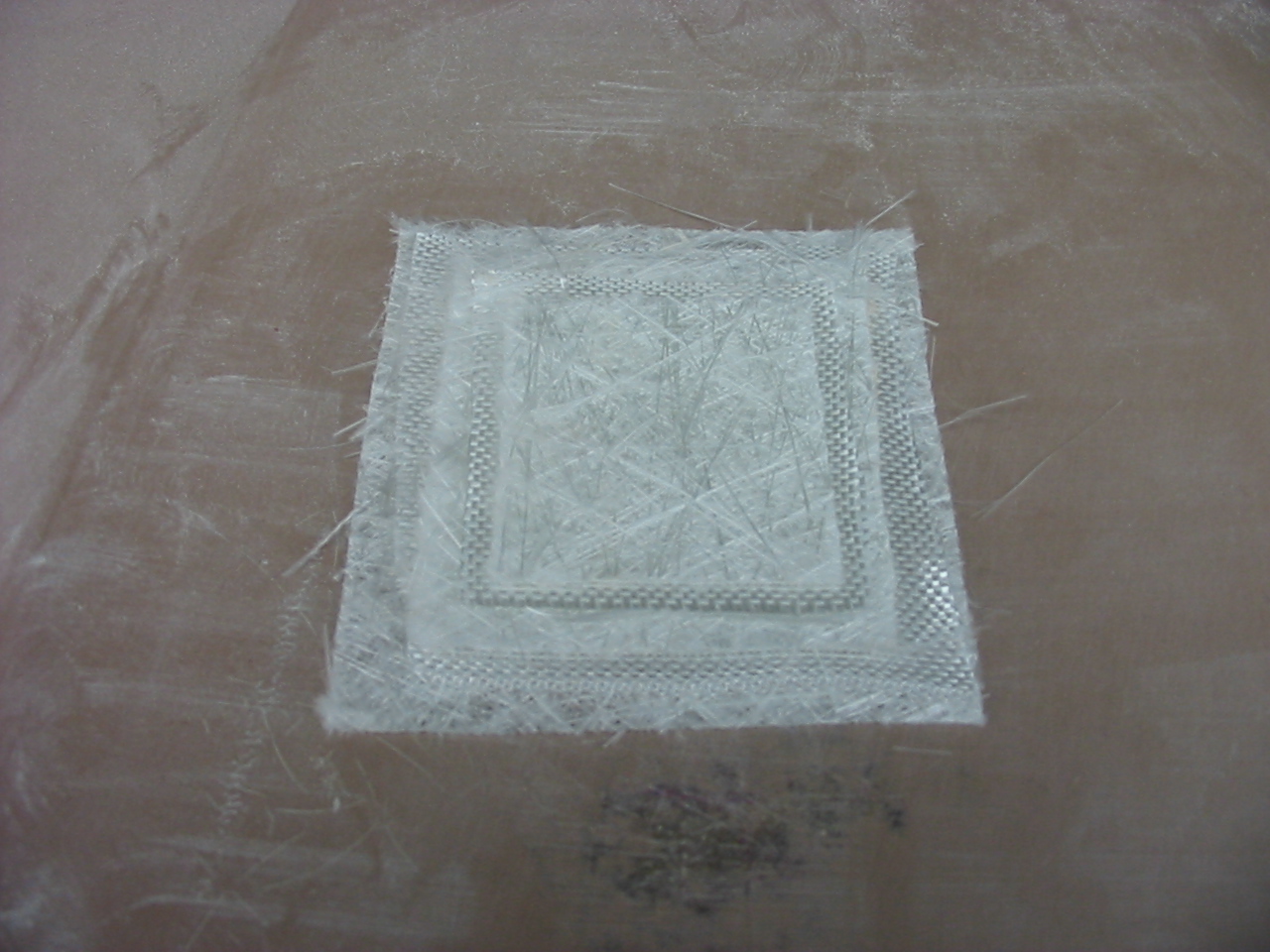
12. Then round off the corners
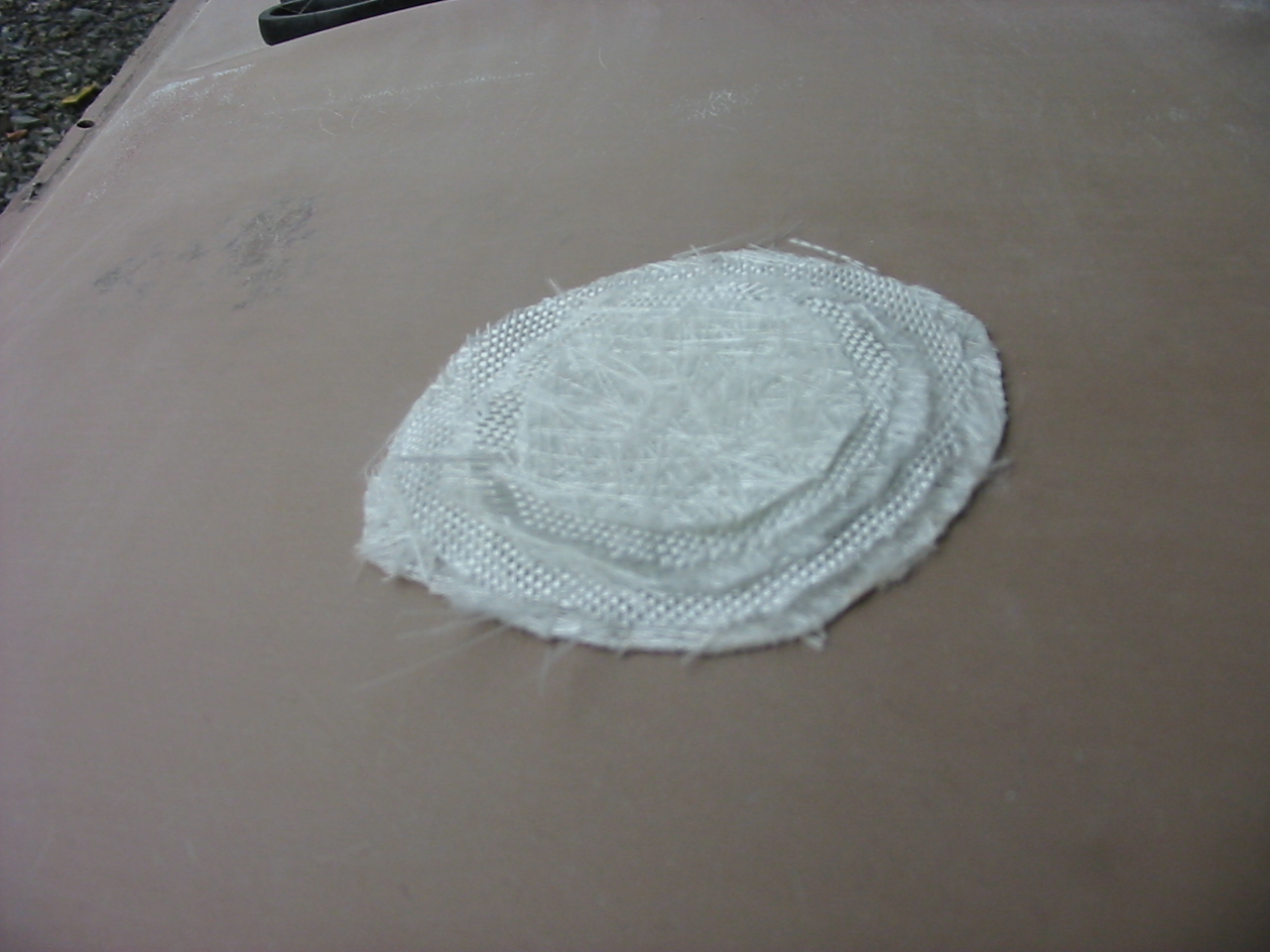
13. Denatured alcohol is used...
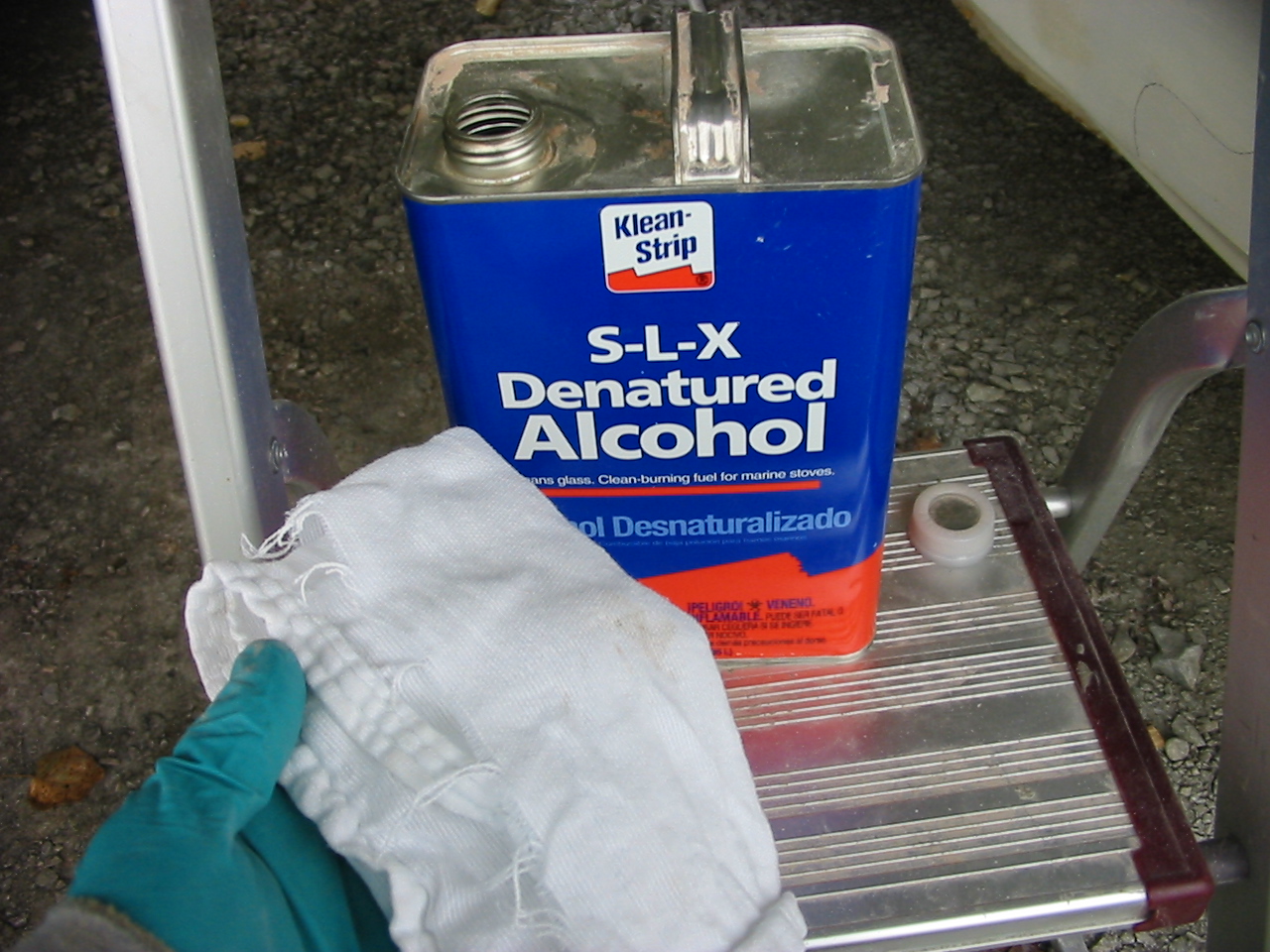
14. ...to clean the repair area.
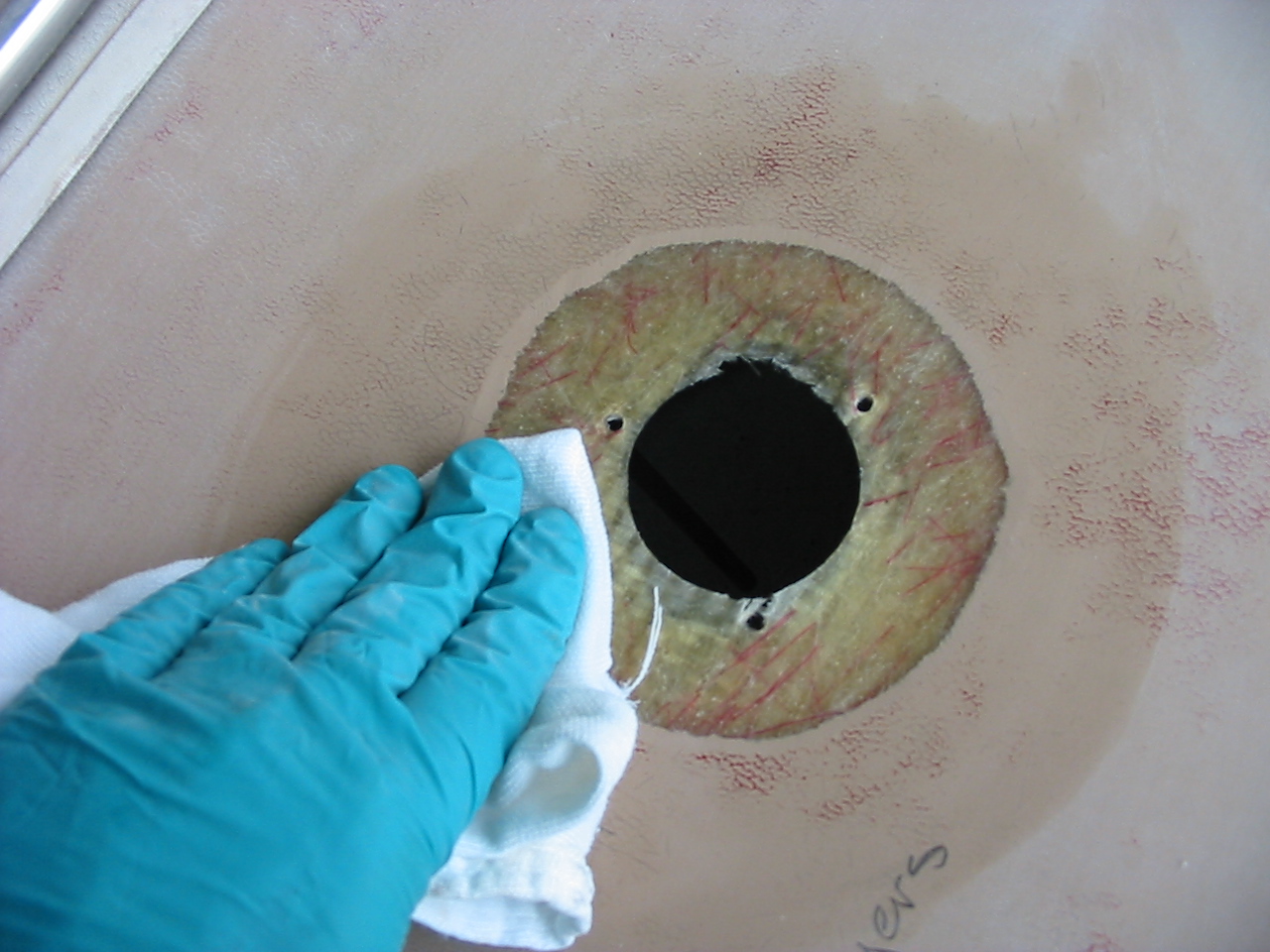
15. The repair must be supported from below to properly compress the layers of fiberglass.
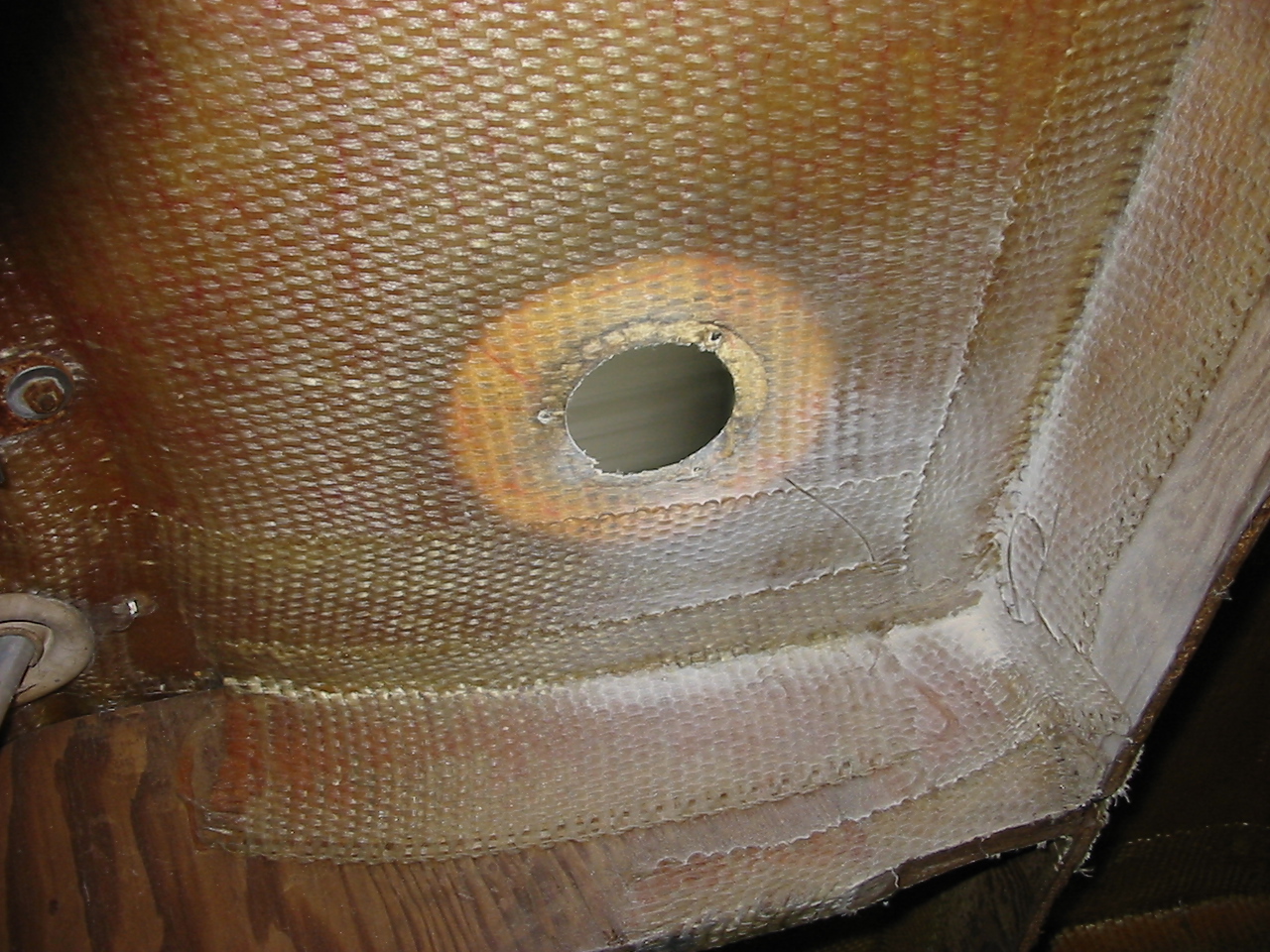
16. A plastic spreader and a scrap piece of pipe does the trick nicely
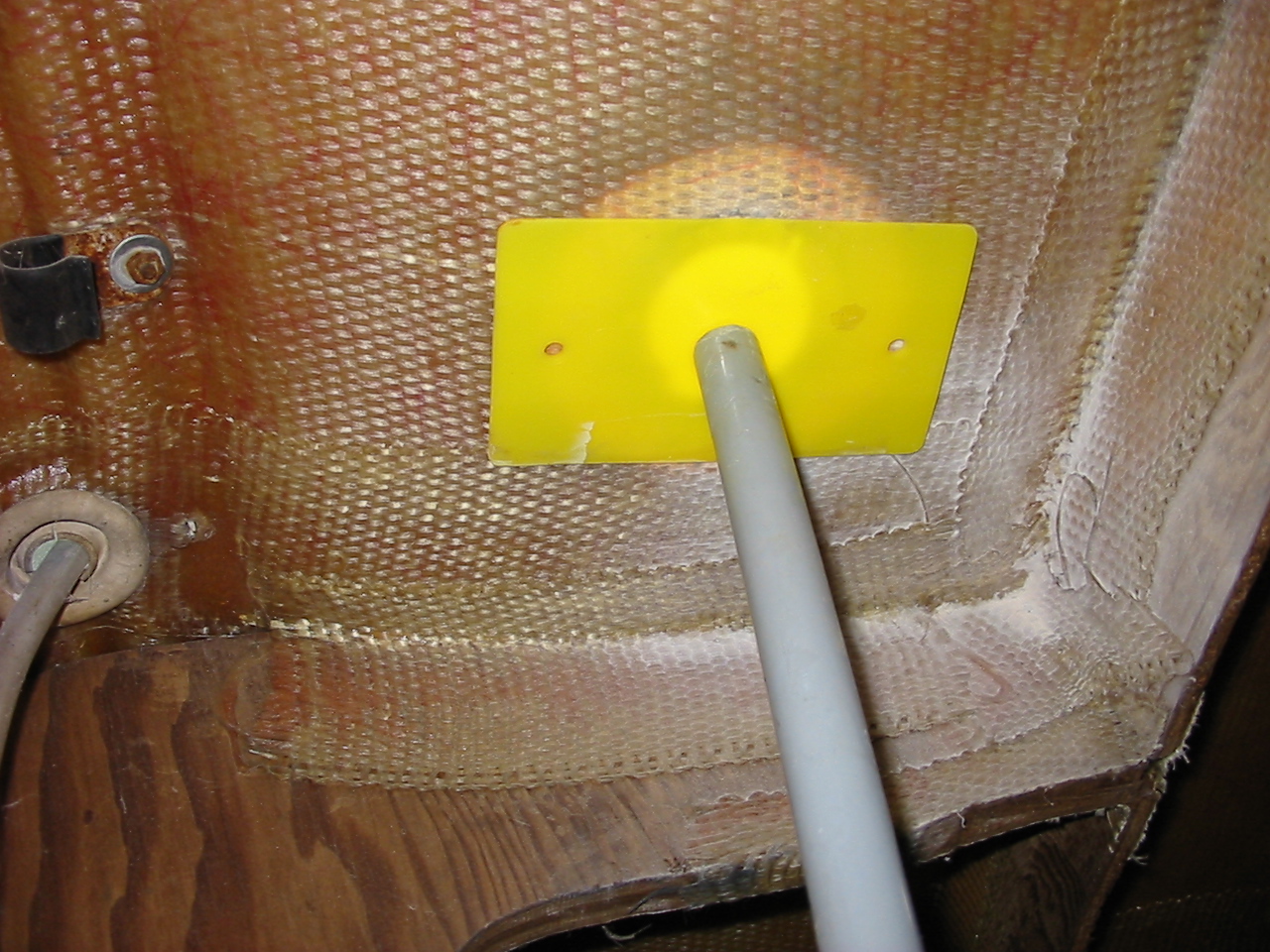
17. The materials. Notice the extra rags and alcohol for clean up.
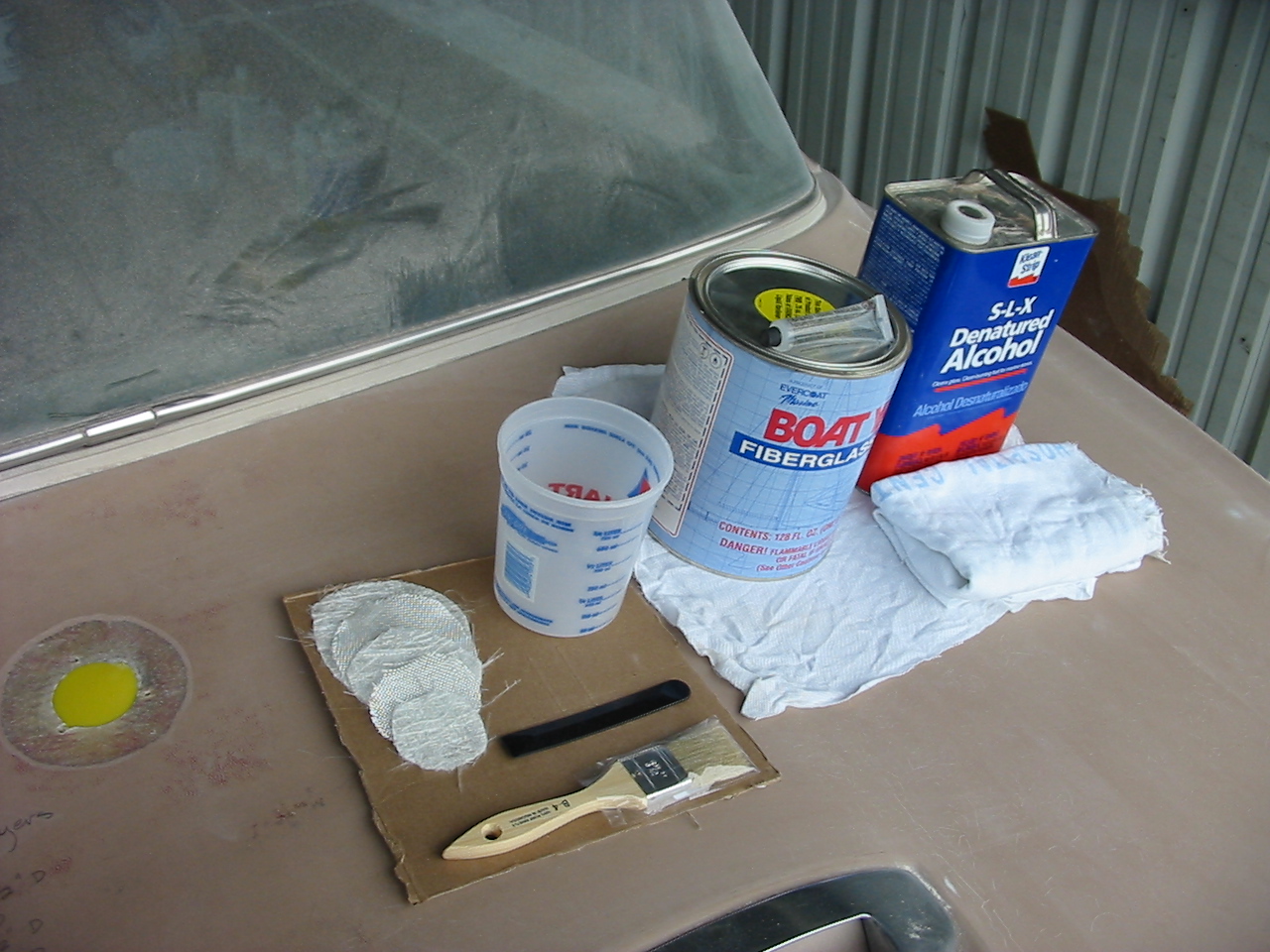
18. Resin is poured, then catalyzed with MEKP at 2% by volume
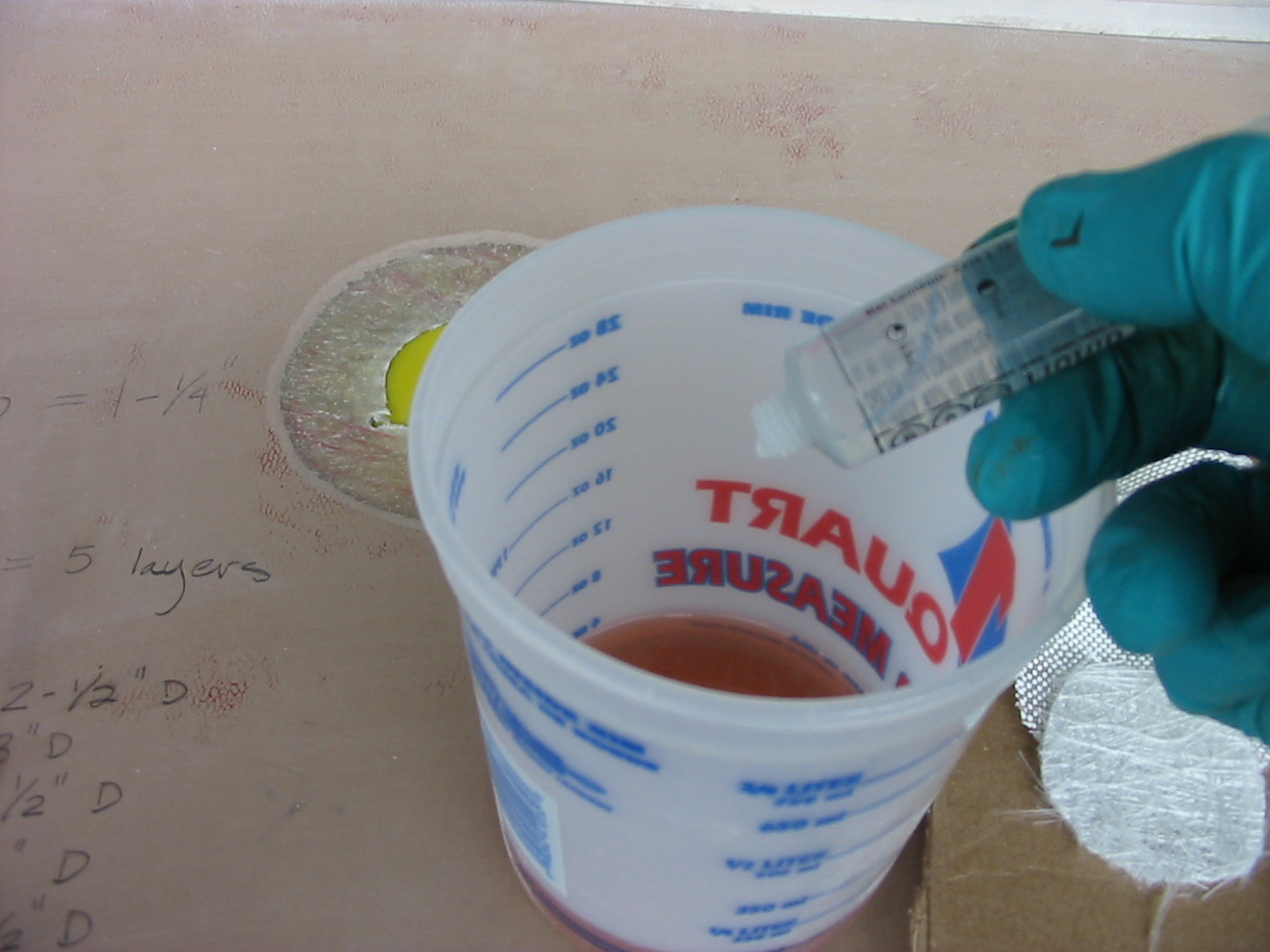
19. Mix the catalyzed resin thoroughly
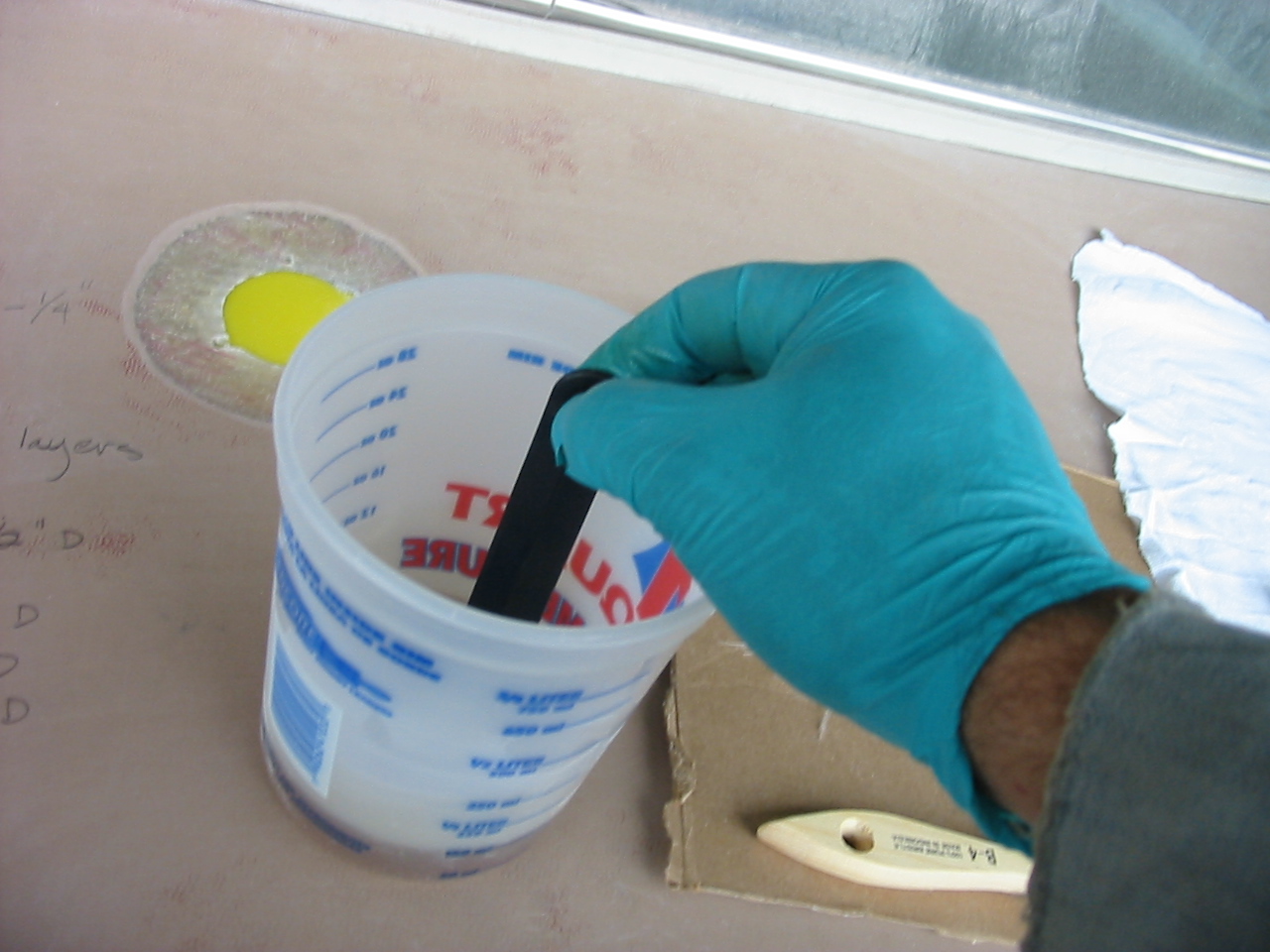
20. Wet the surface area with resin.
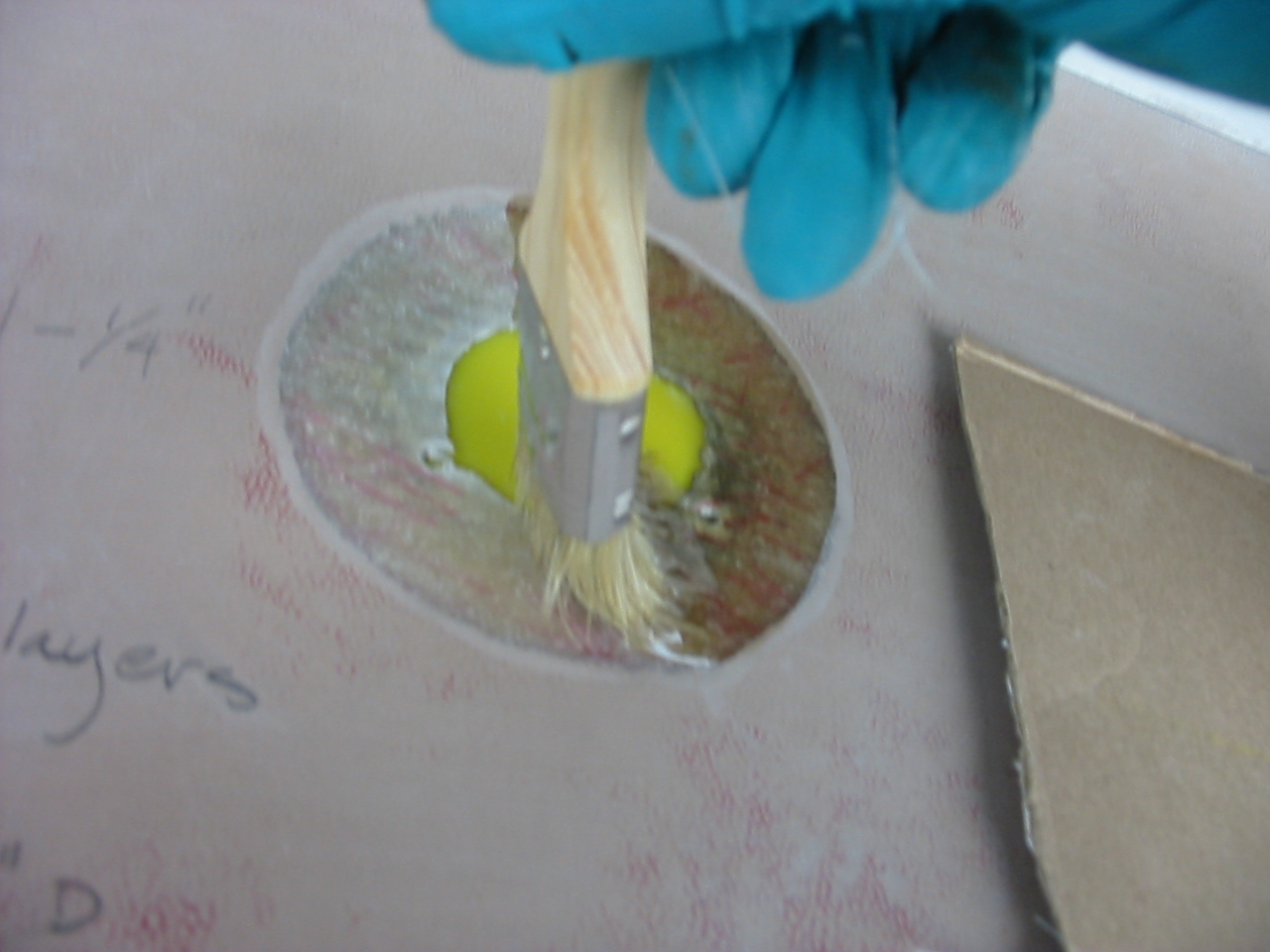
21. Then wet out and add each layer to the repair. Compress the layers with a resin roller or by stipling with a brush.
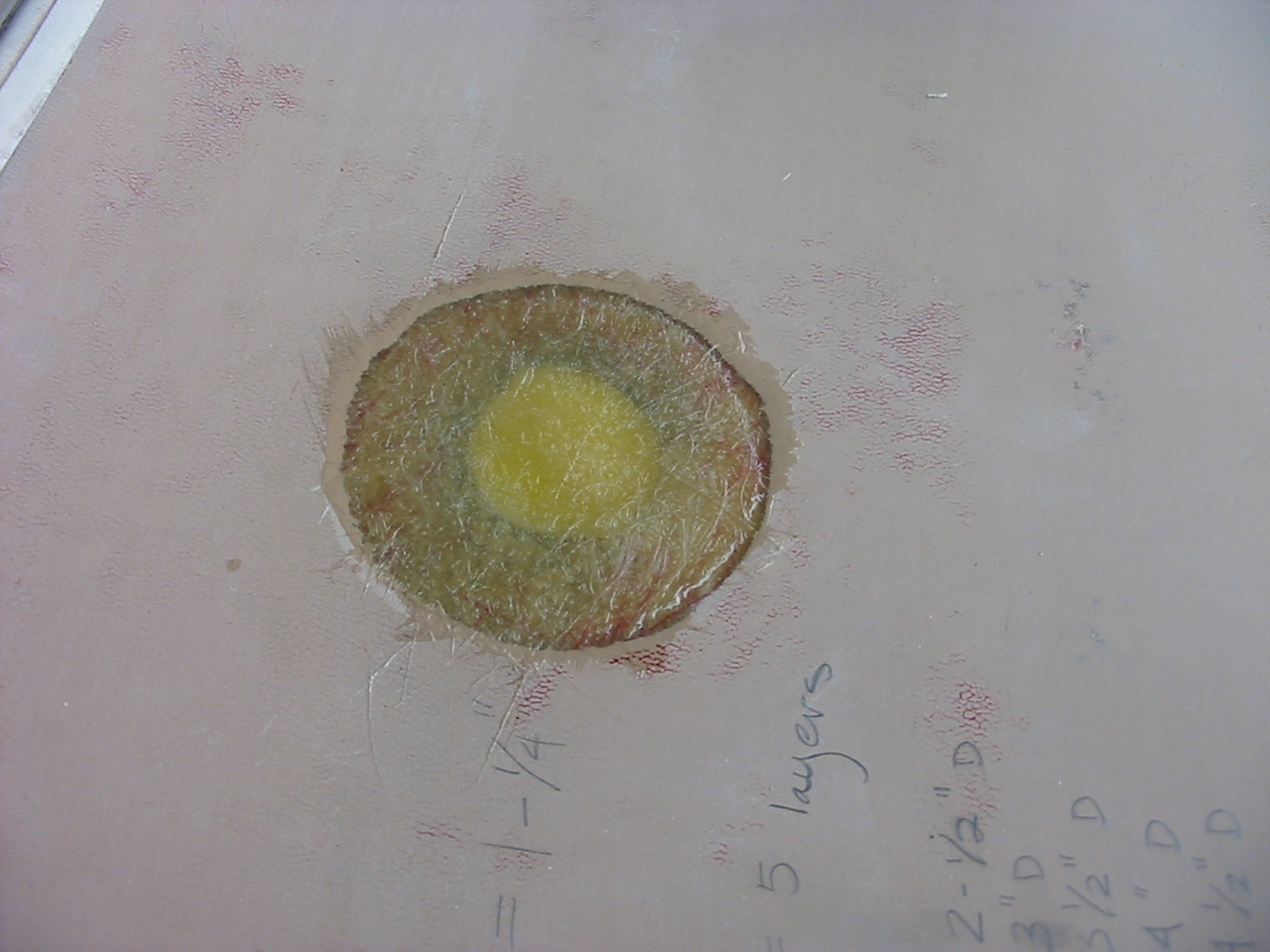
22. Excess resin can be cleaned up with alcohol or acetone. Always wear gloves with acetone
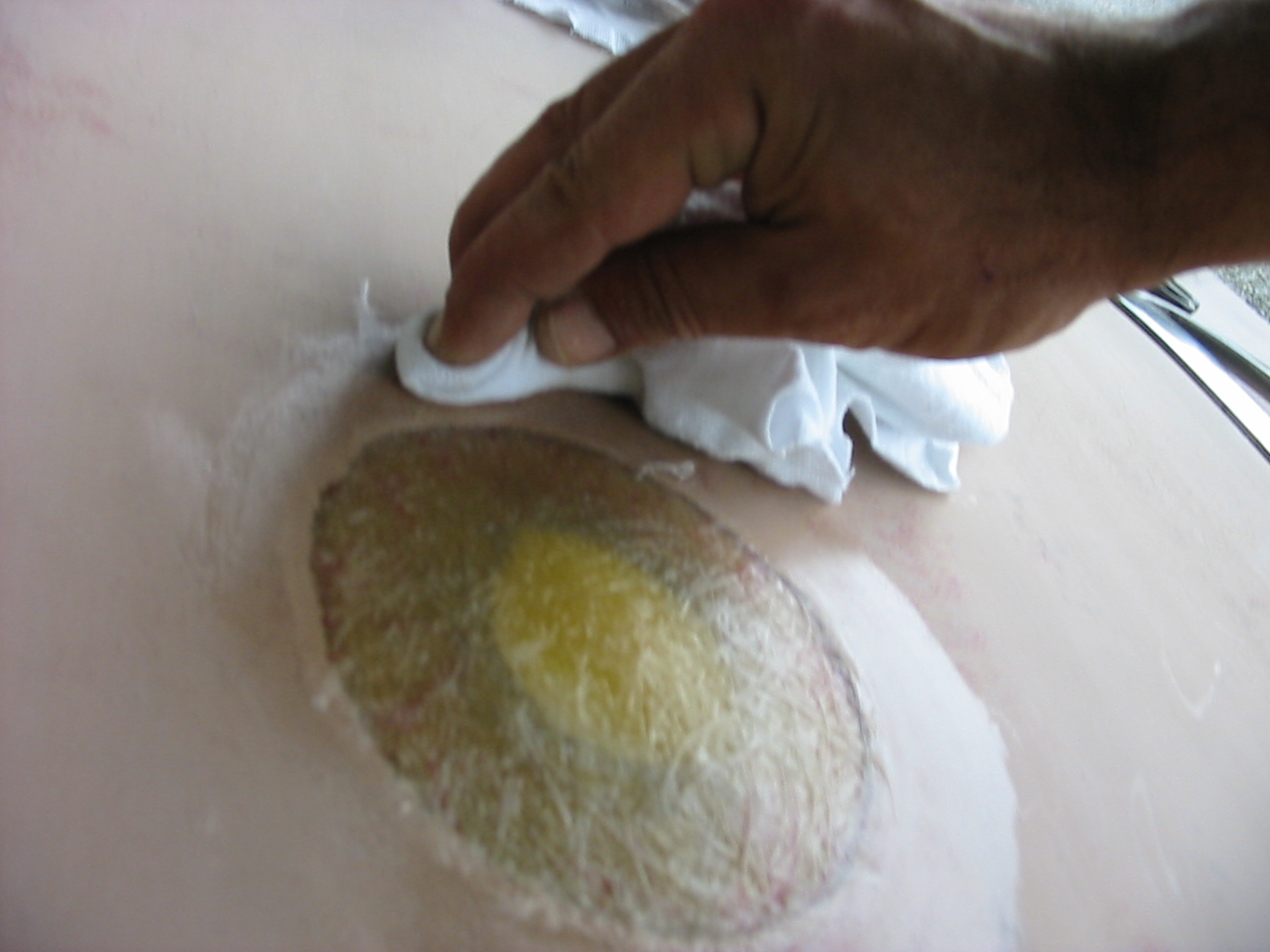
23. Once the fiberglass has kicked, cover surface imperfections with fairing filler
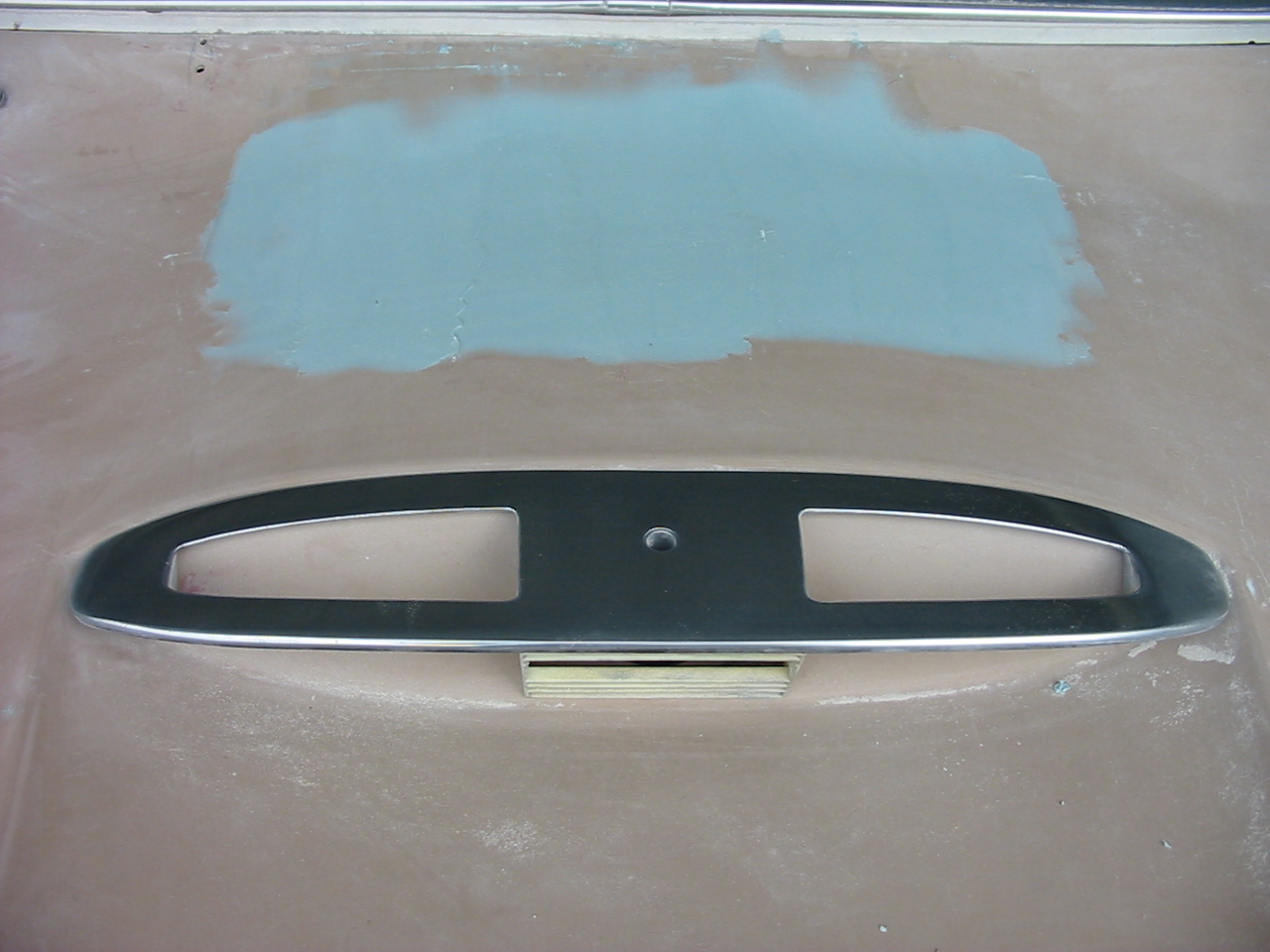
24. Sand it flush and fair. Voila! No more hole.
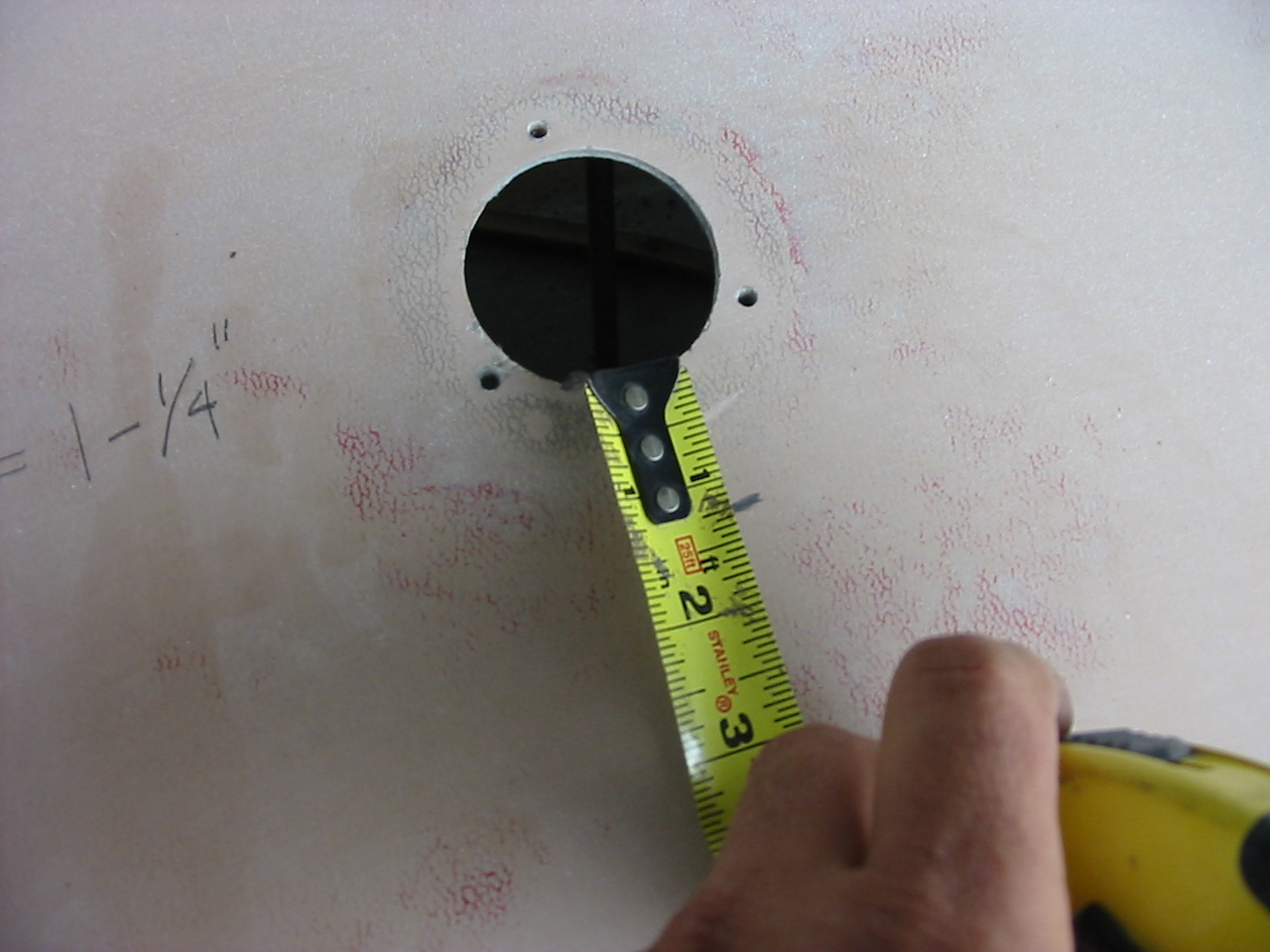
4. Connecting the hash marks
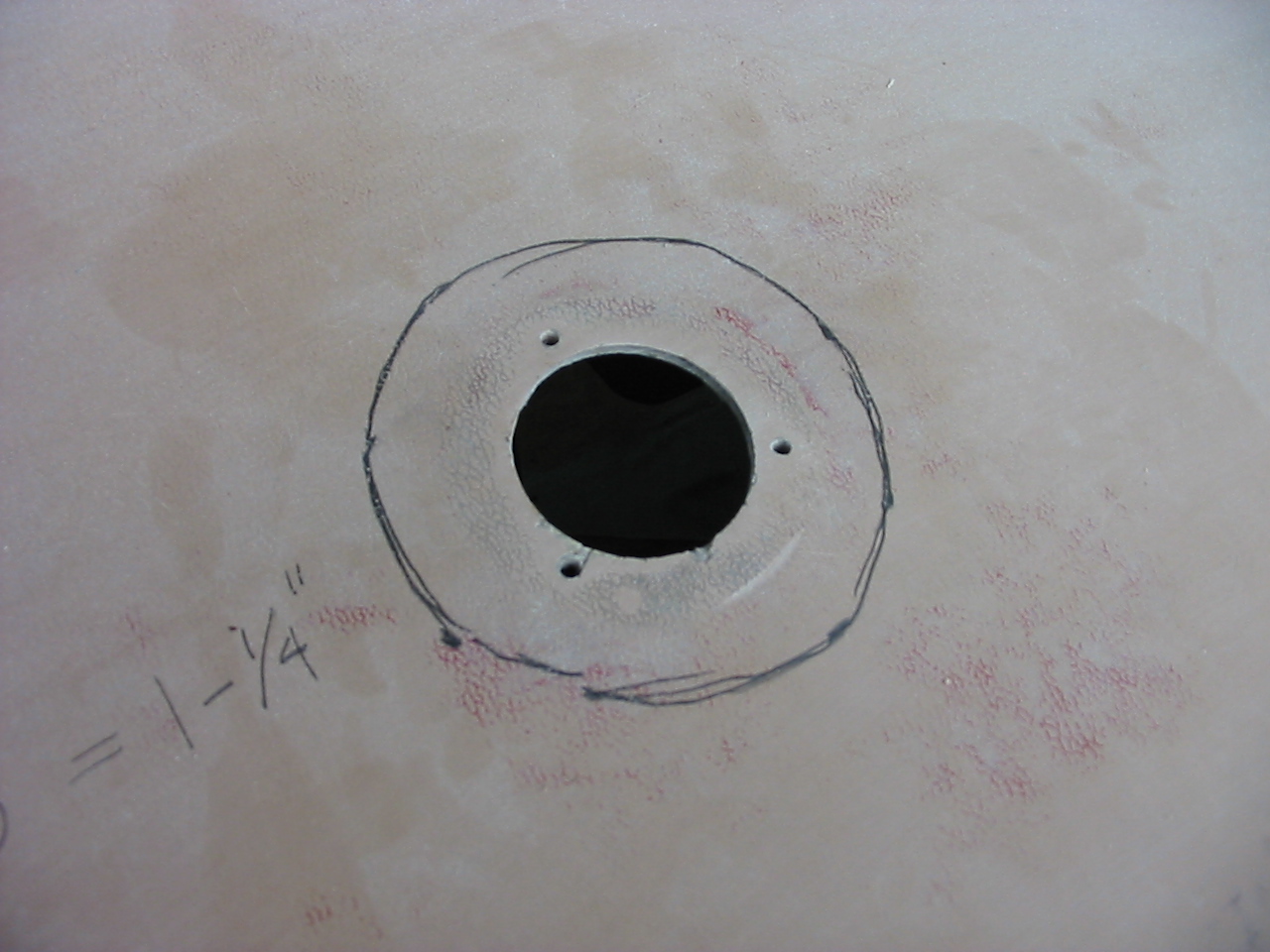
5. A grinder with an 80 grit flap wheel will give me a nice smooth taper
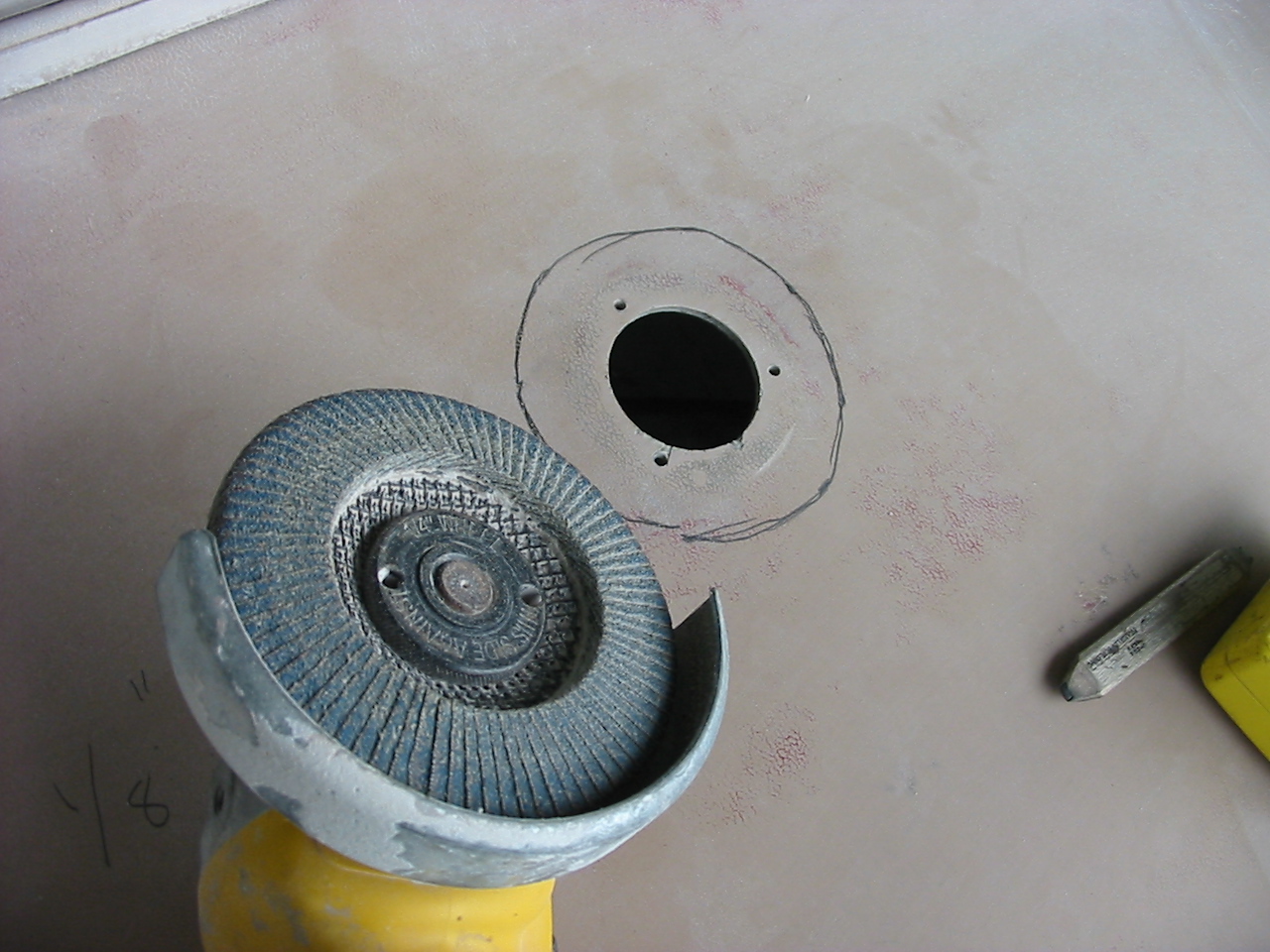
6. As always, protect yourself (safety glasses too)
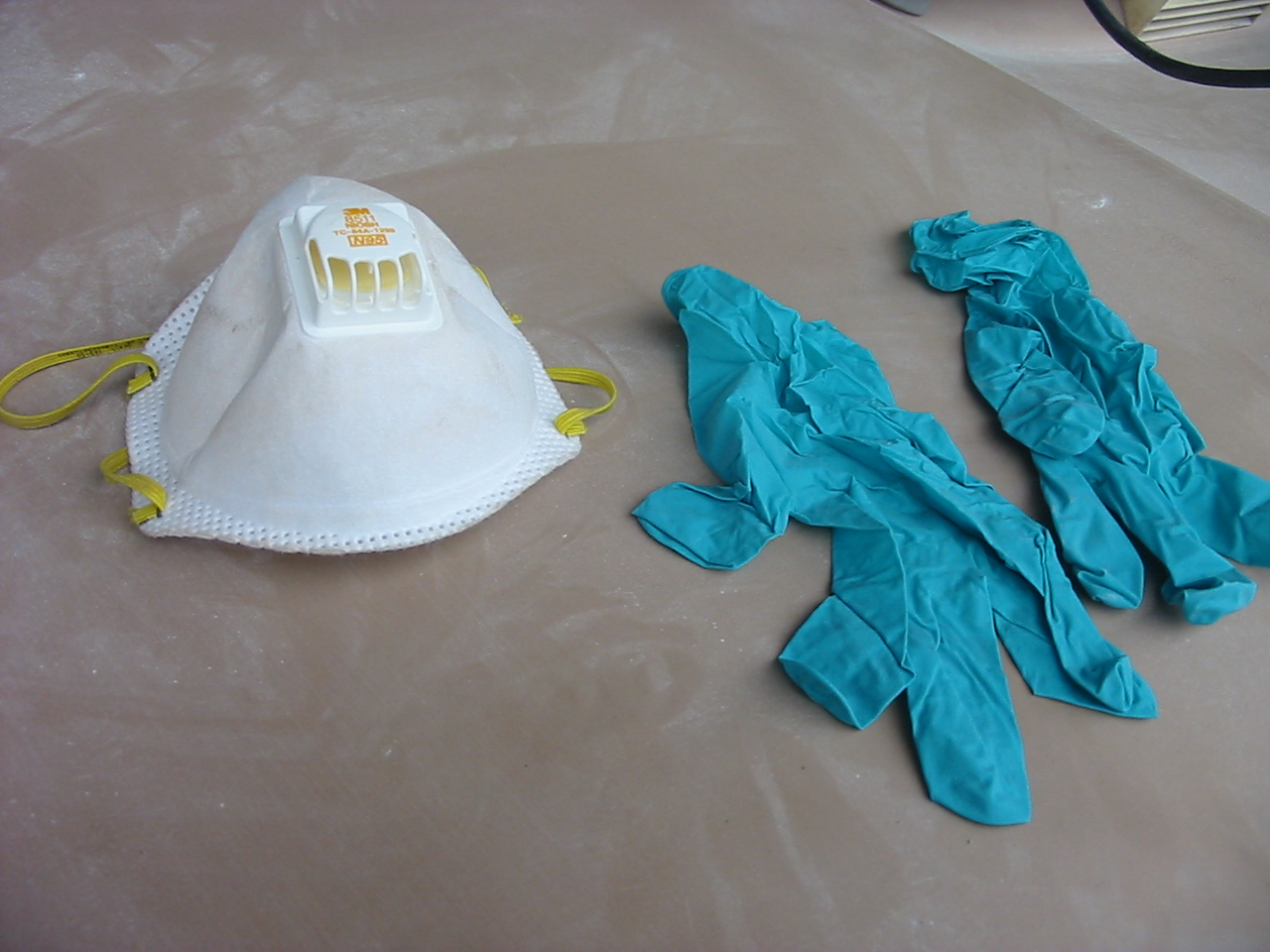
7. The repair area tapered back at a 10:1 ratio
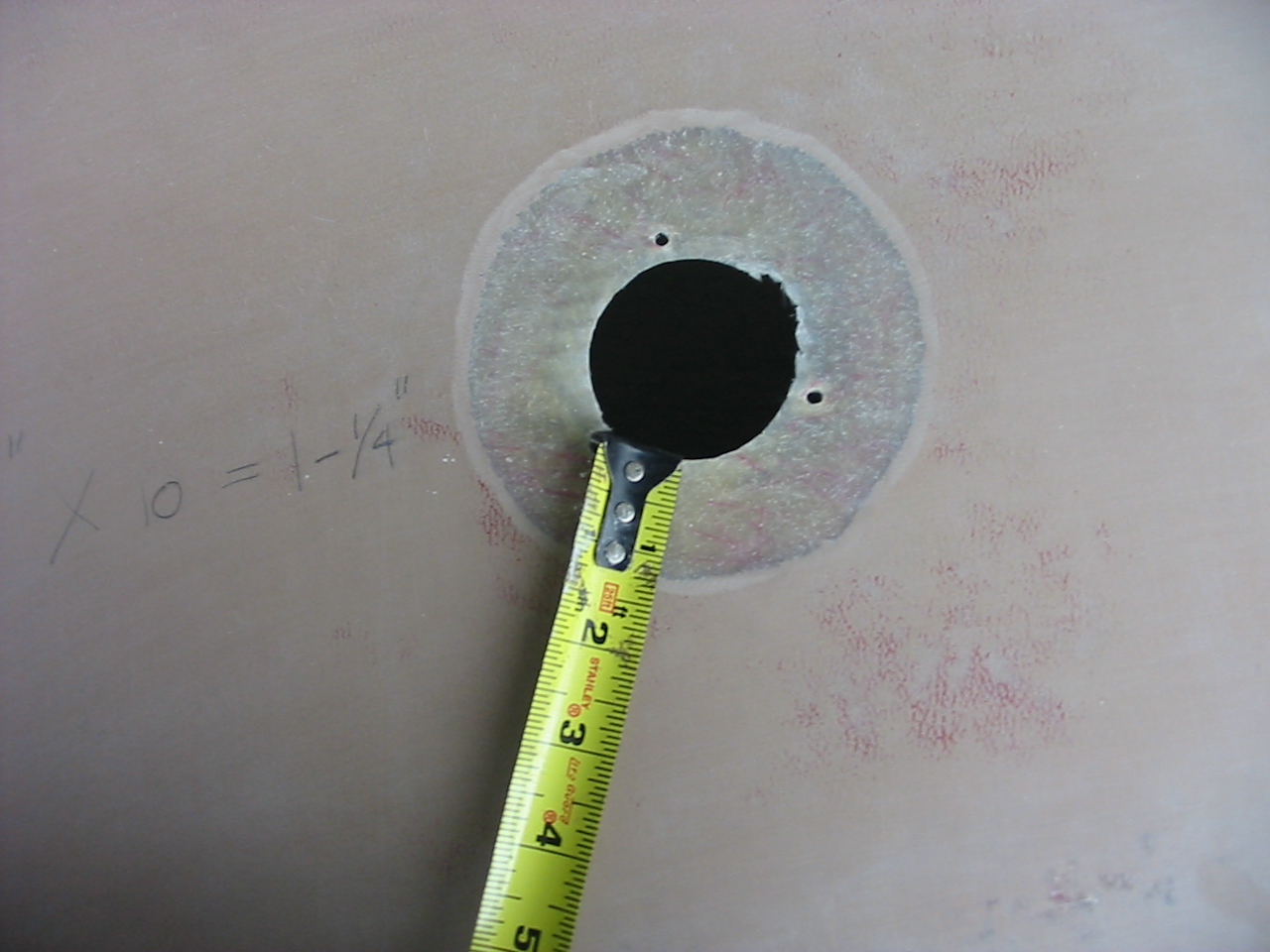
8. Which makes the total repair 4-1/2" in diameter
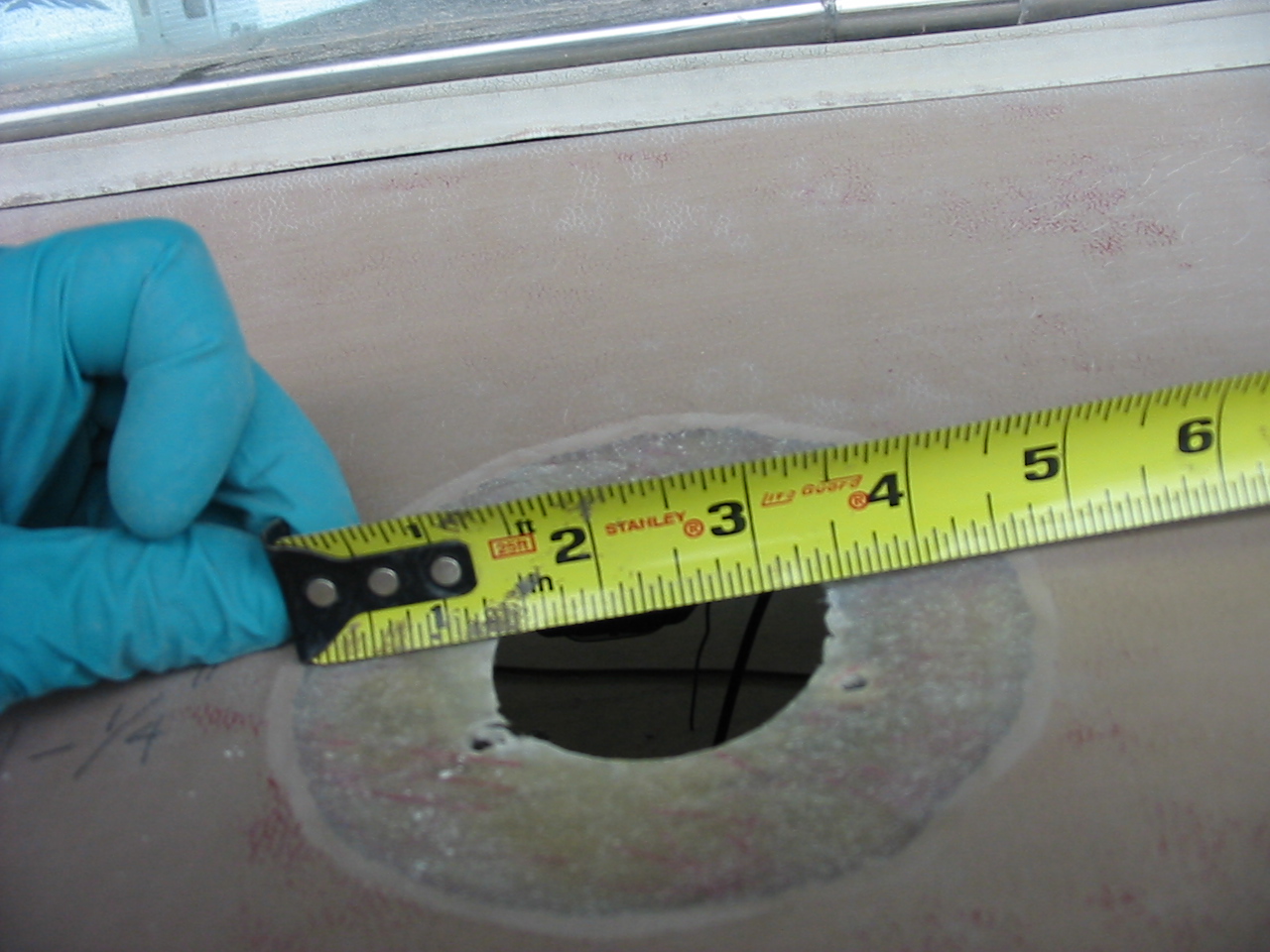
9. Each layer of fiberglass should extend 1/4" beyond the previous layer
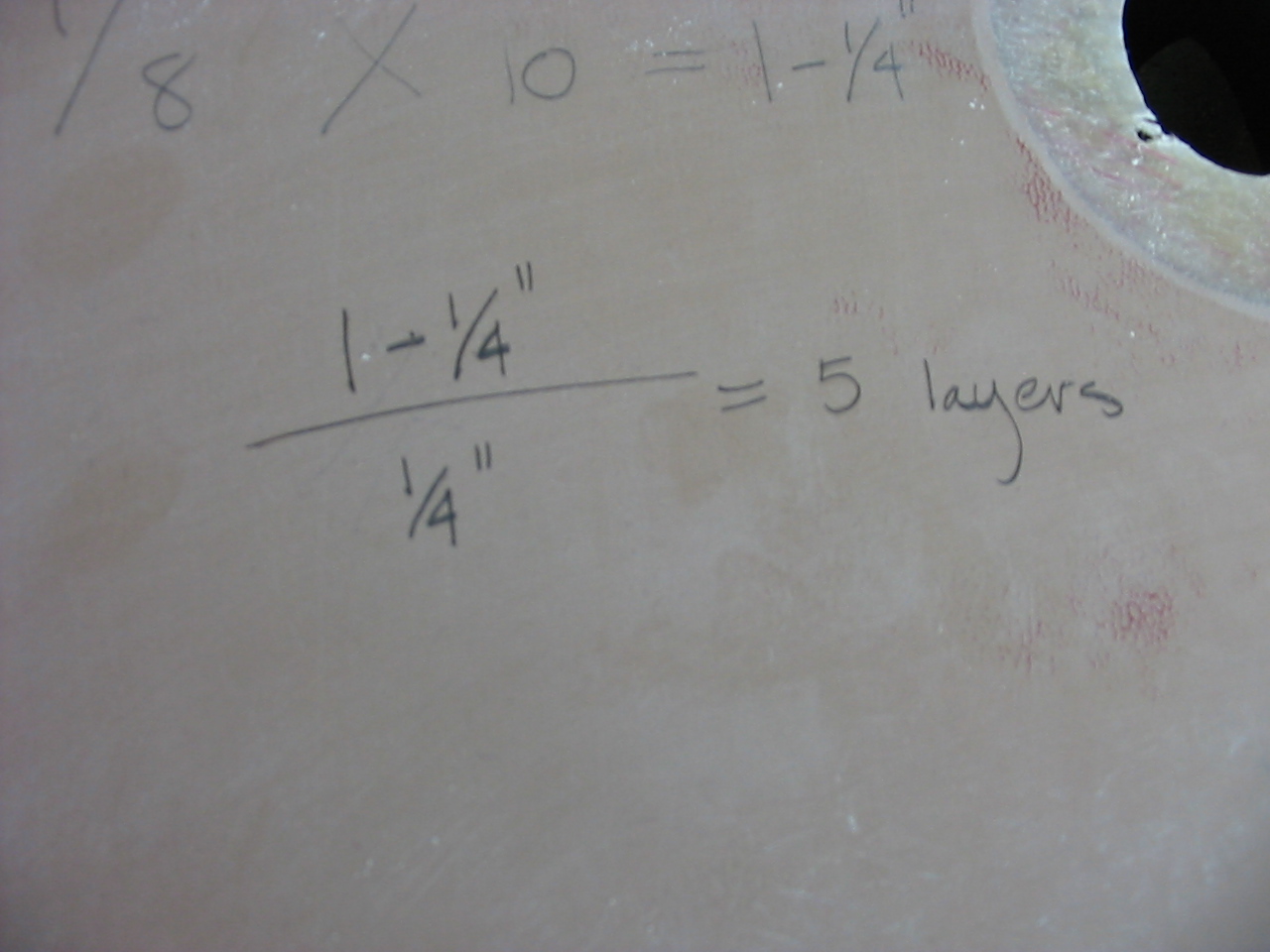
10. My fiberglass lay up schedule. Always alternate with layers of mat. Always finish with a layer of mat.

11. The fiberglass cut to a measured square.
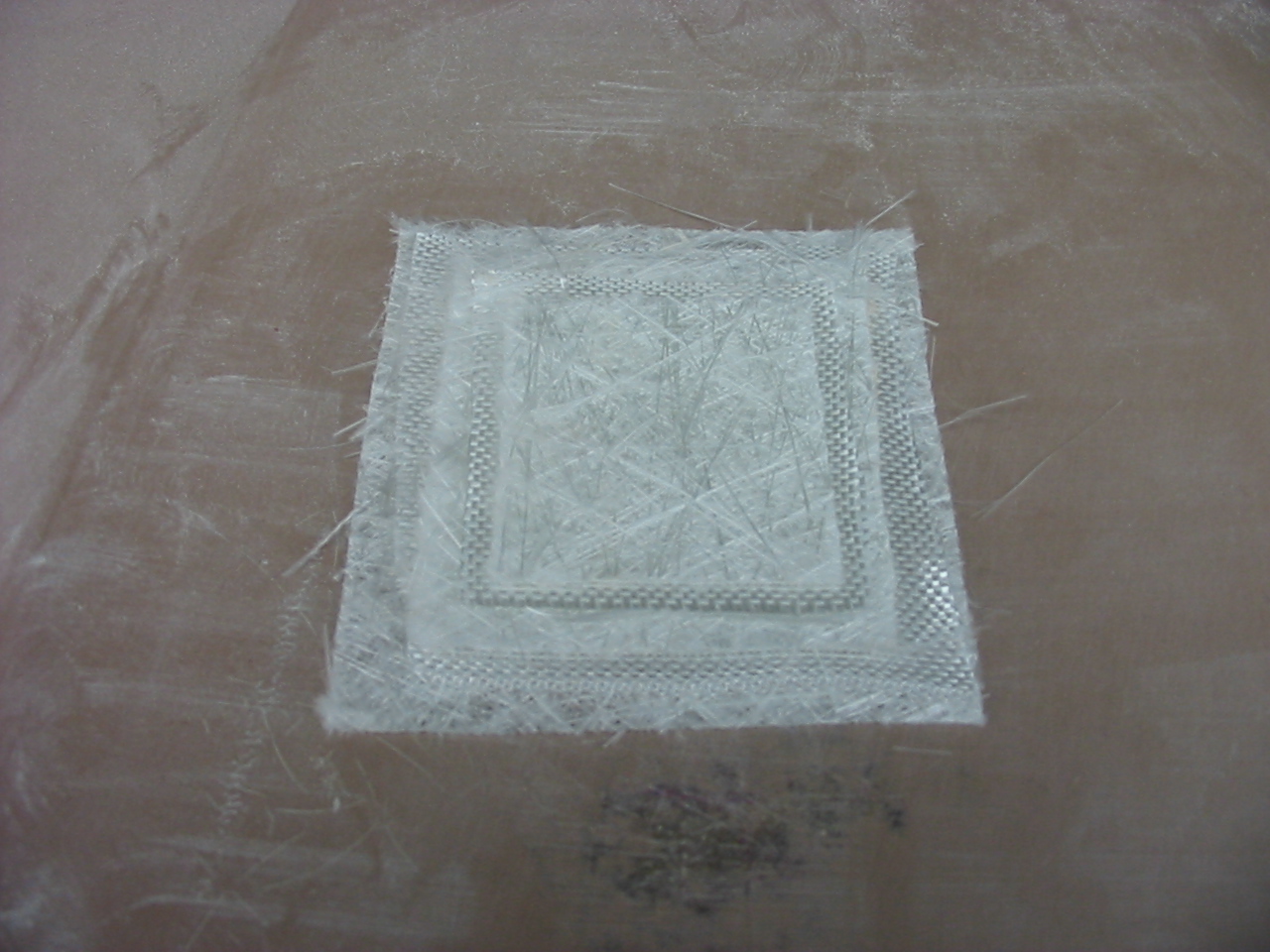
12. Then round off the corners
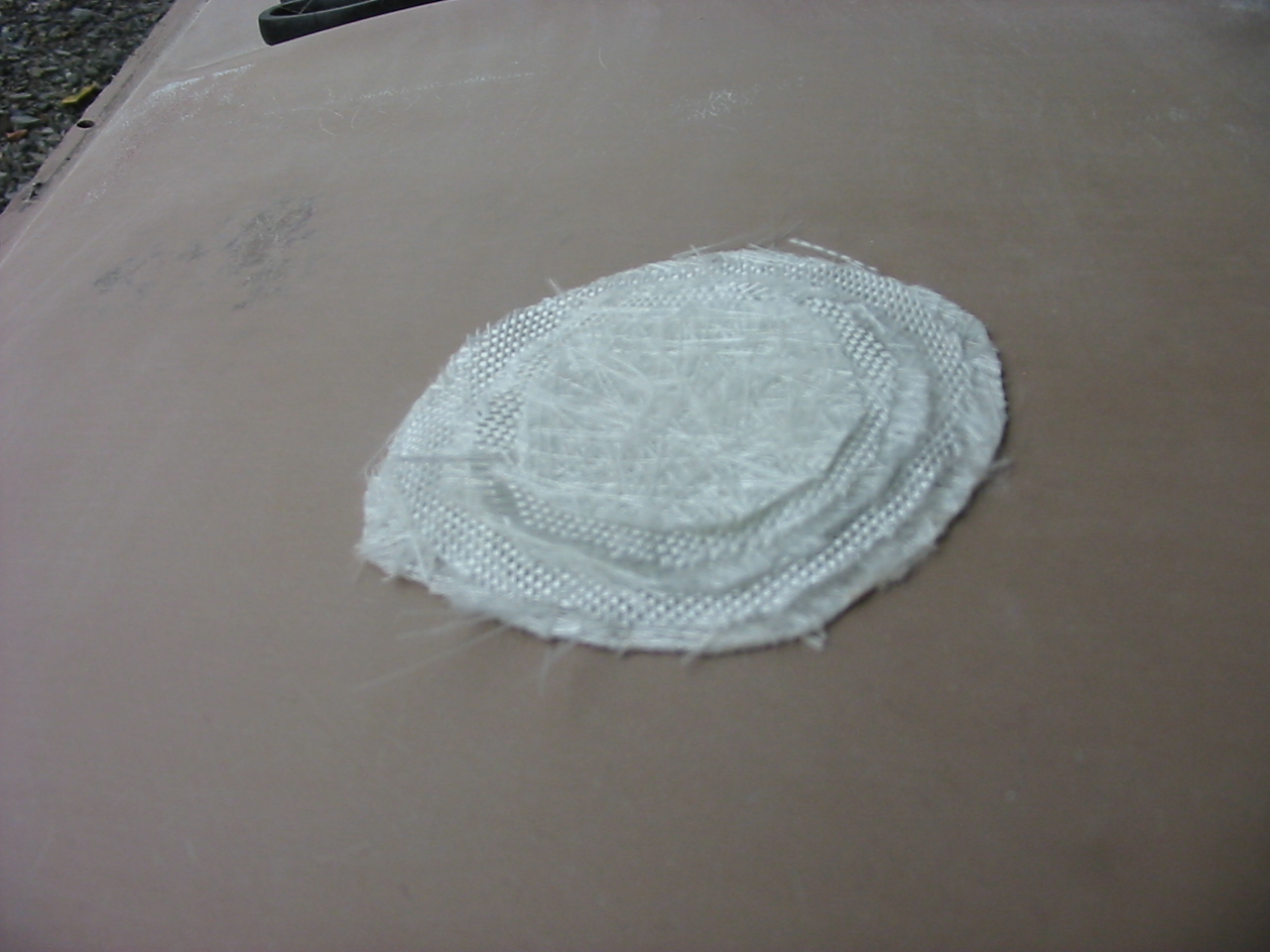
13. Denatured alcohol is used...
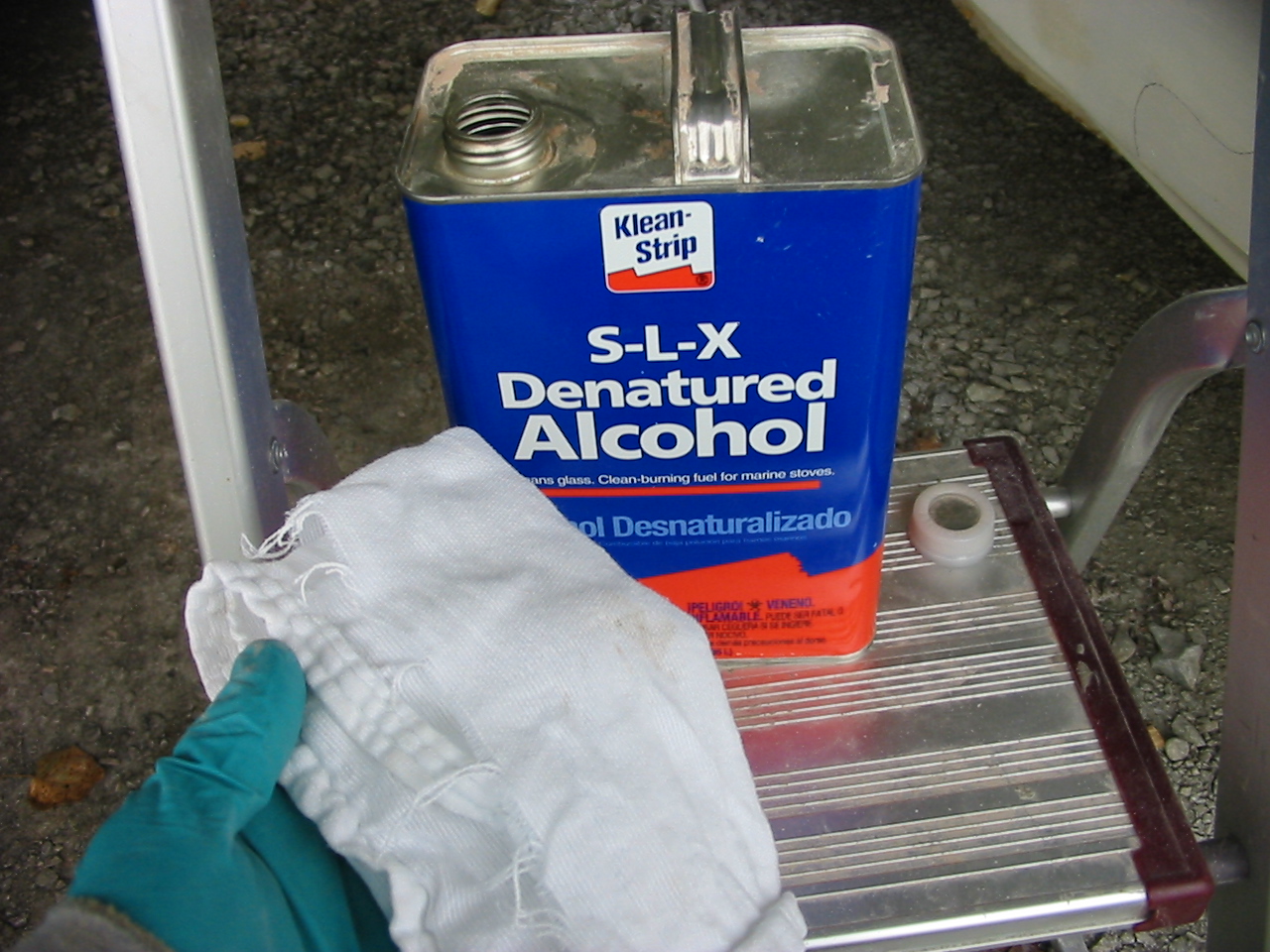
14. ...to clean the repair area.
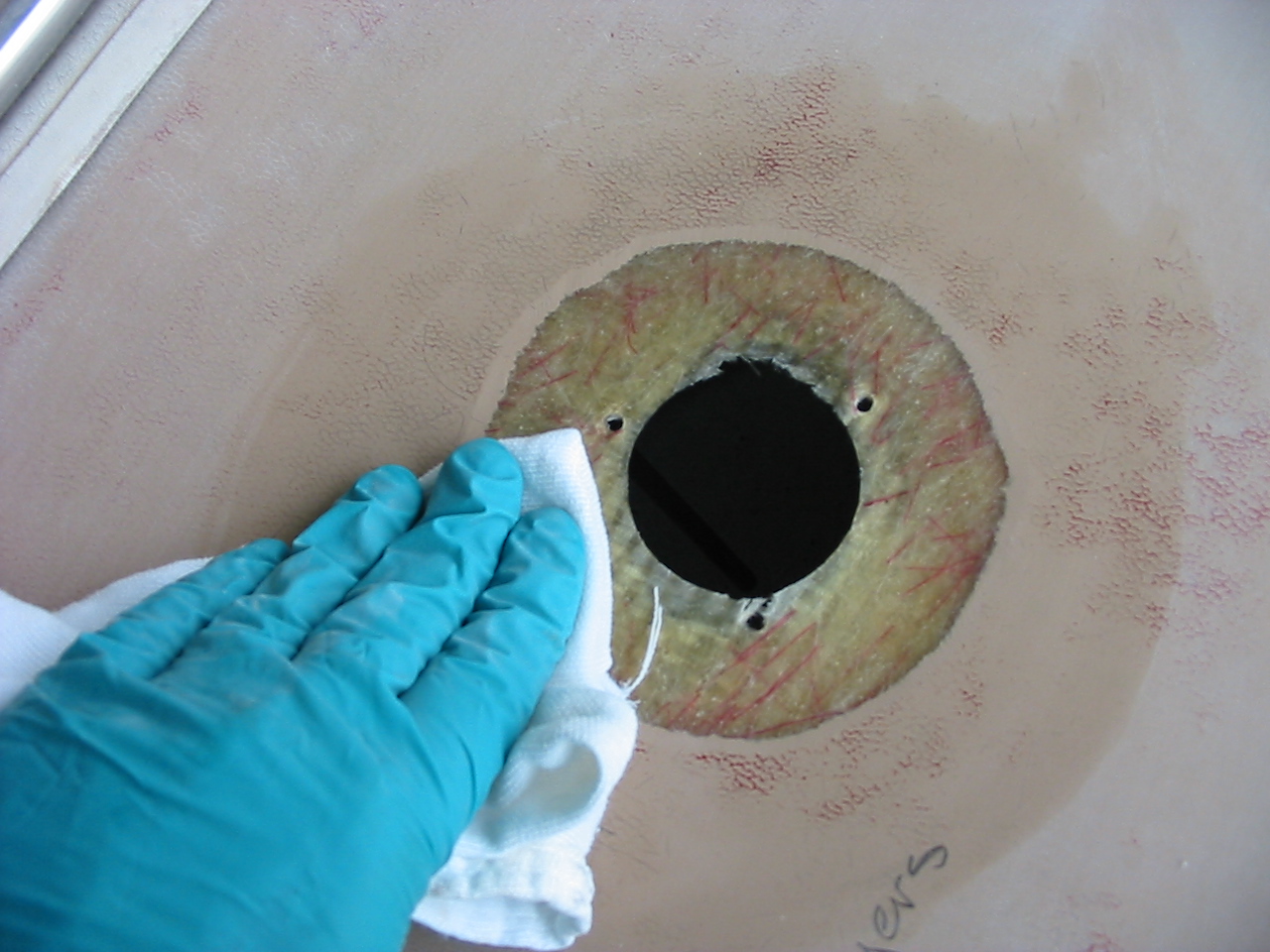
15. The repair must be supported from below to properly compress the layers of fiberglass.
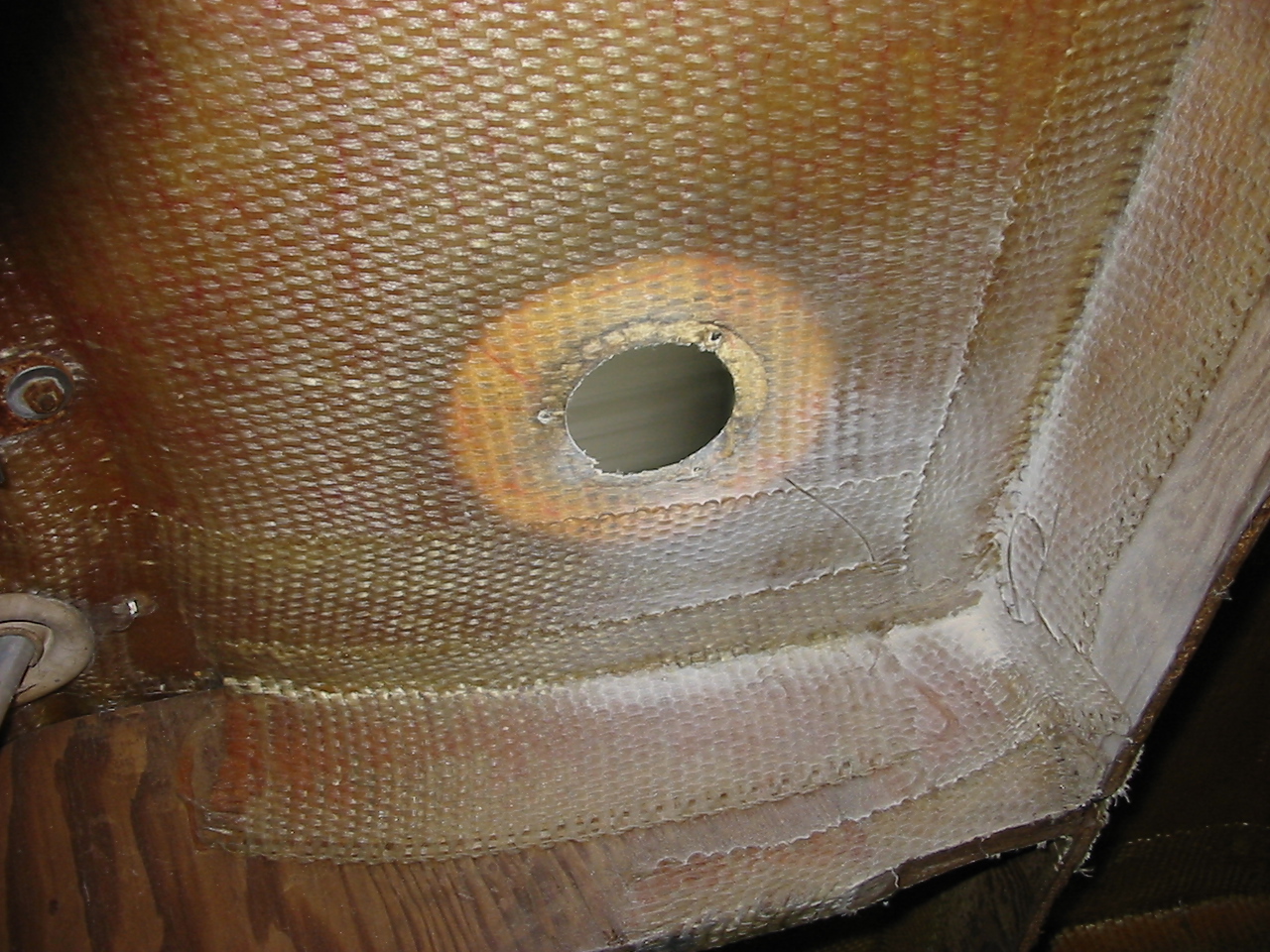
16. A plastic spreader and a scrap piece of pipe does the trick nicely
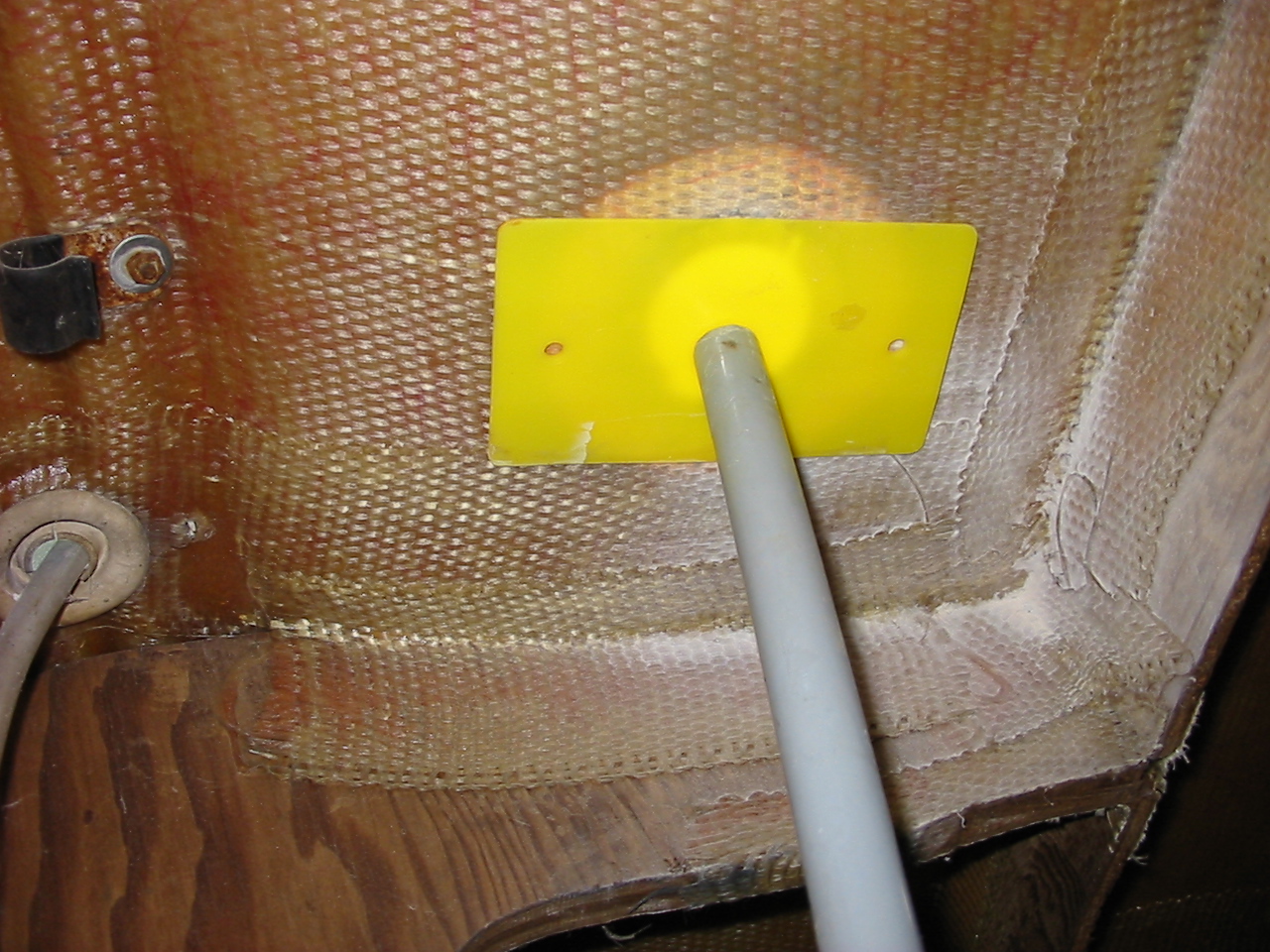
17. The materials. Notice the extra rags and alcohol for clean up.
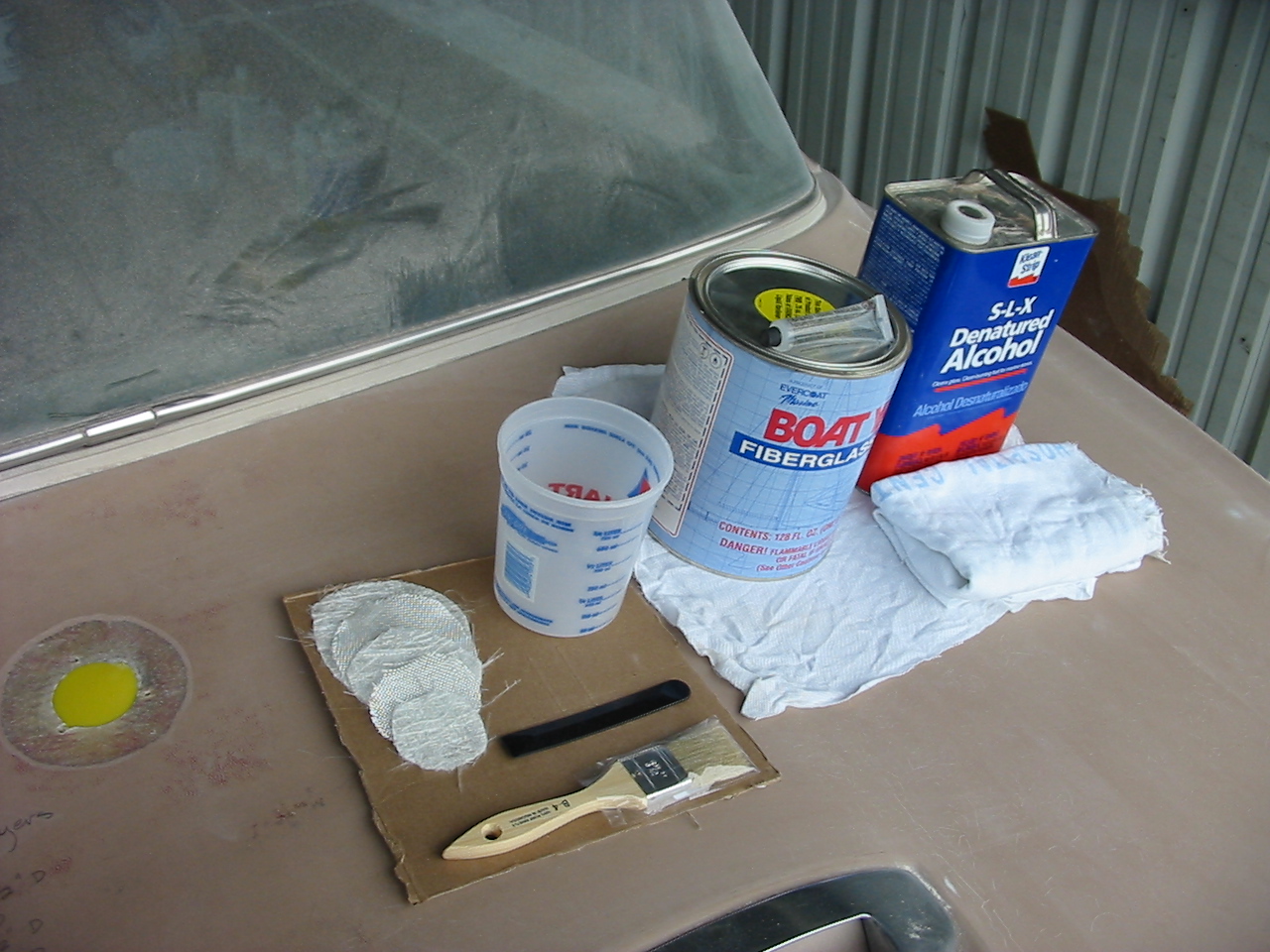
18. Resin is poured, then catalyzed with MEKP at 2% by volume
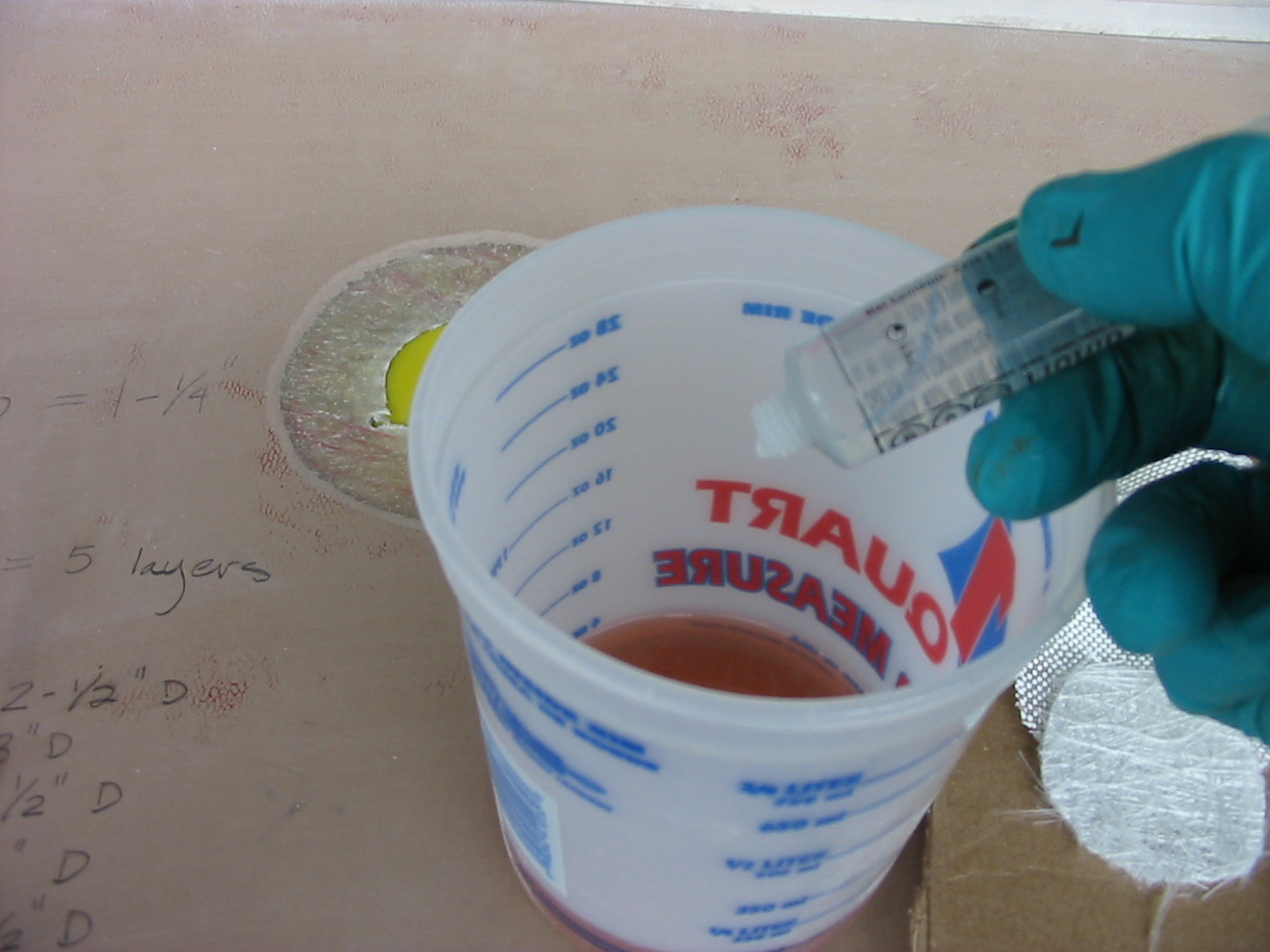
19. Mix the catalyzed resin thoroughly
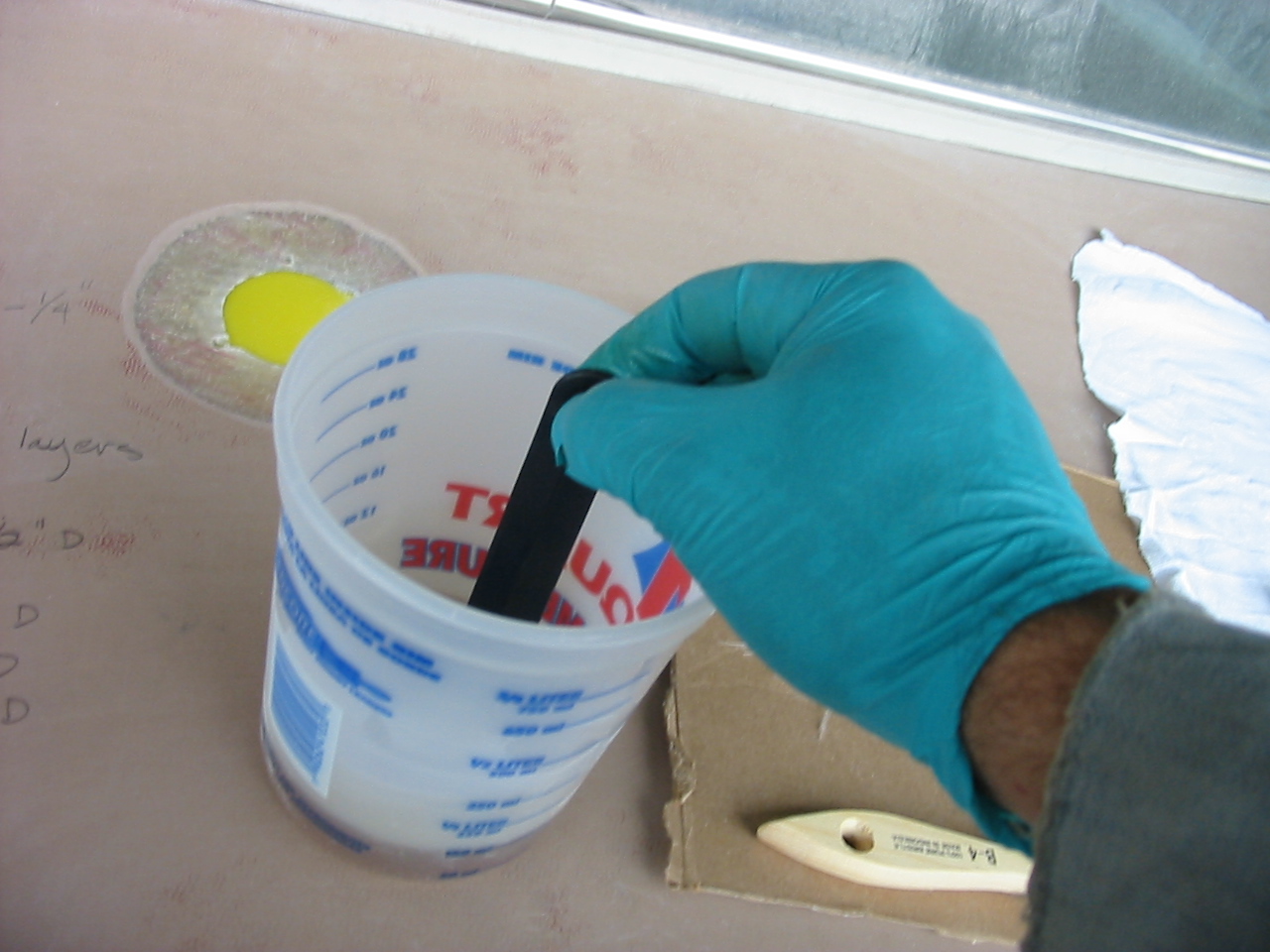
20. Wet the surface area with resin.
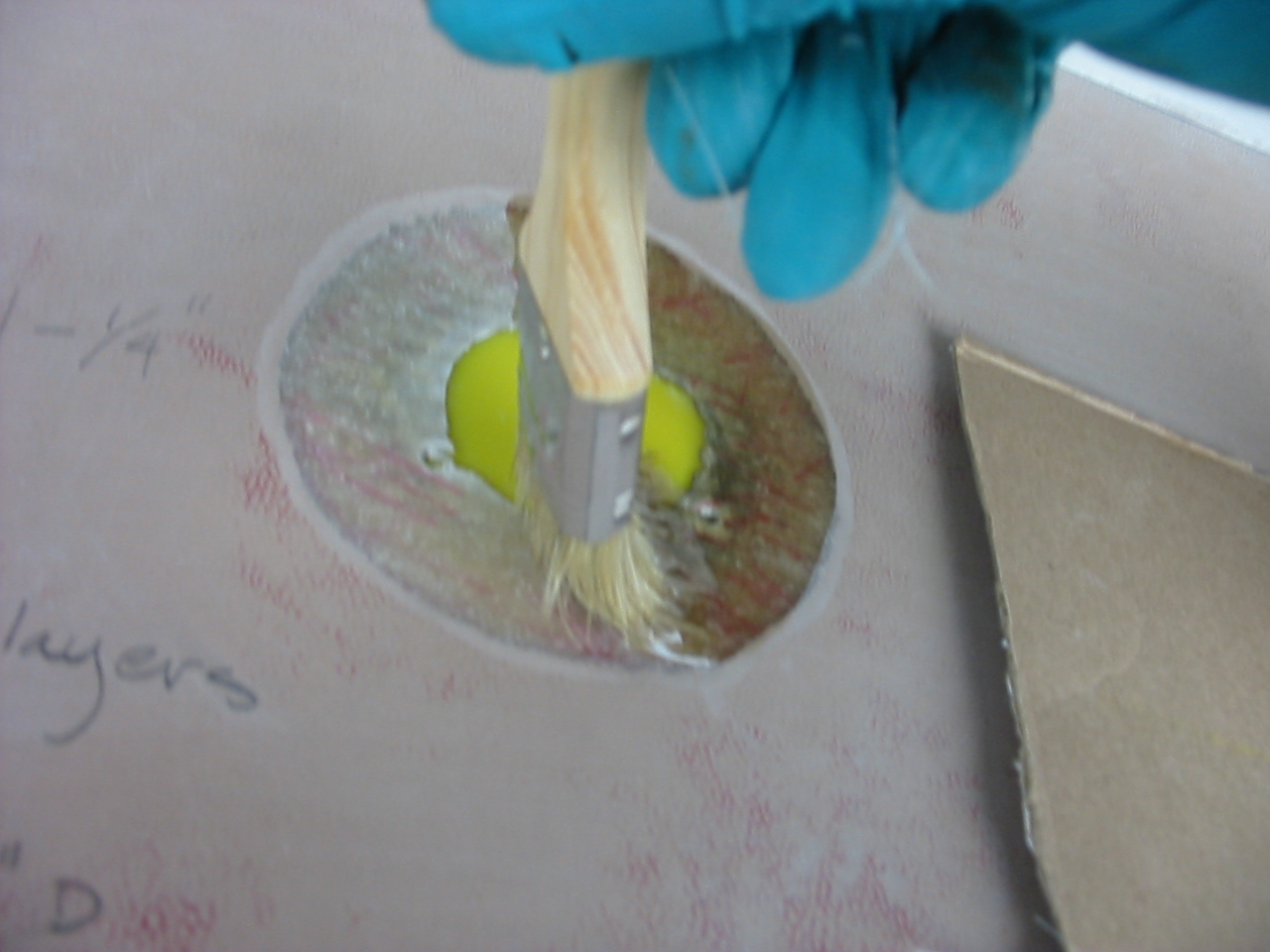
21. Then wet out and add each layer to the repair. Compress the layers with a resin roller or by stipling with a brush.
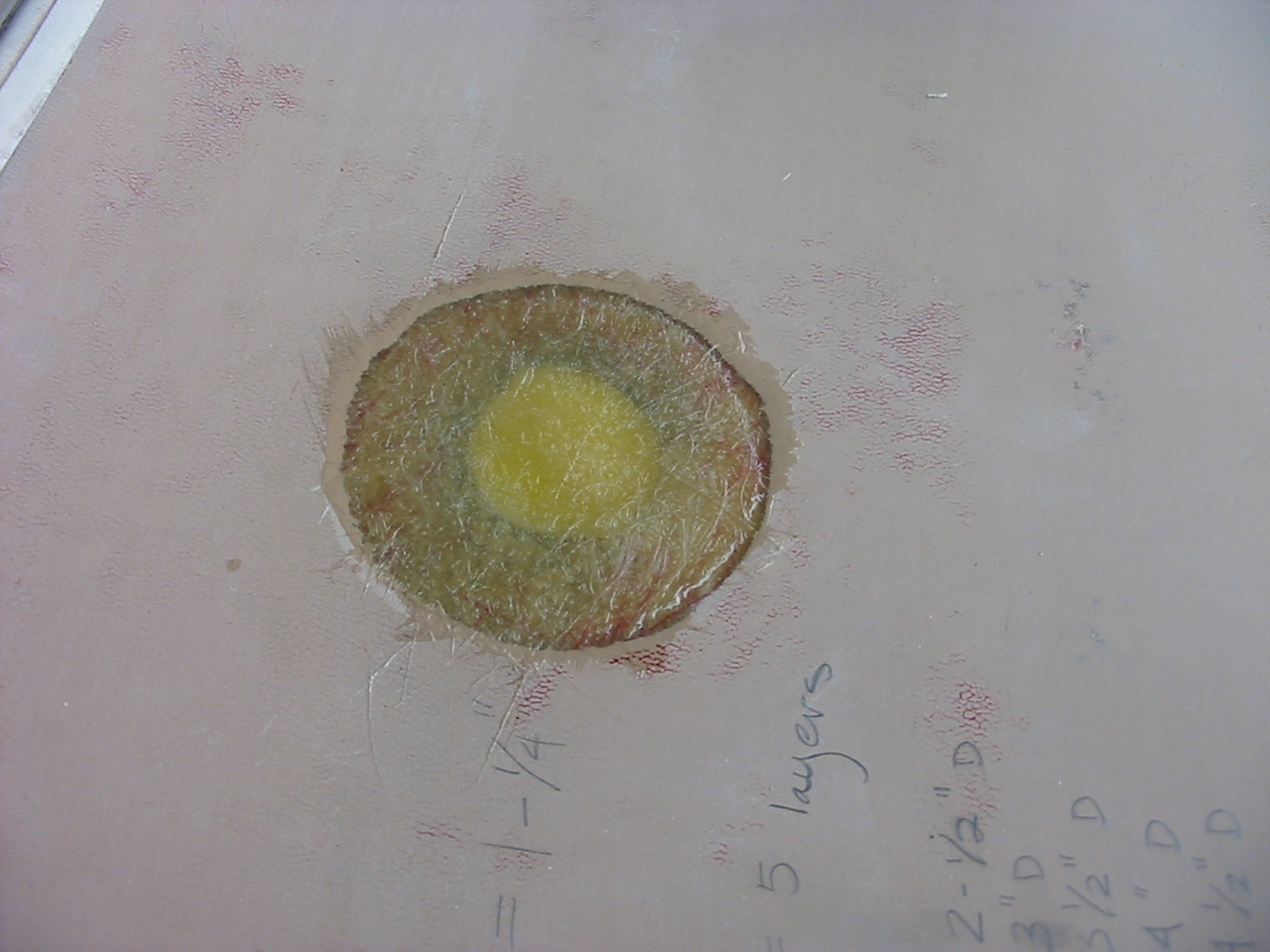
22. Excess resin can be cleaned up with alcohol or acetone. Always wear gloves with acetone
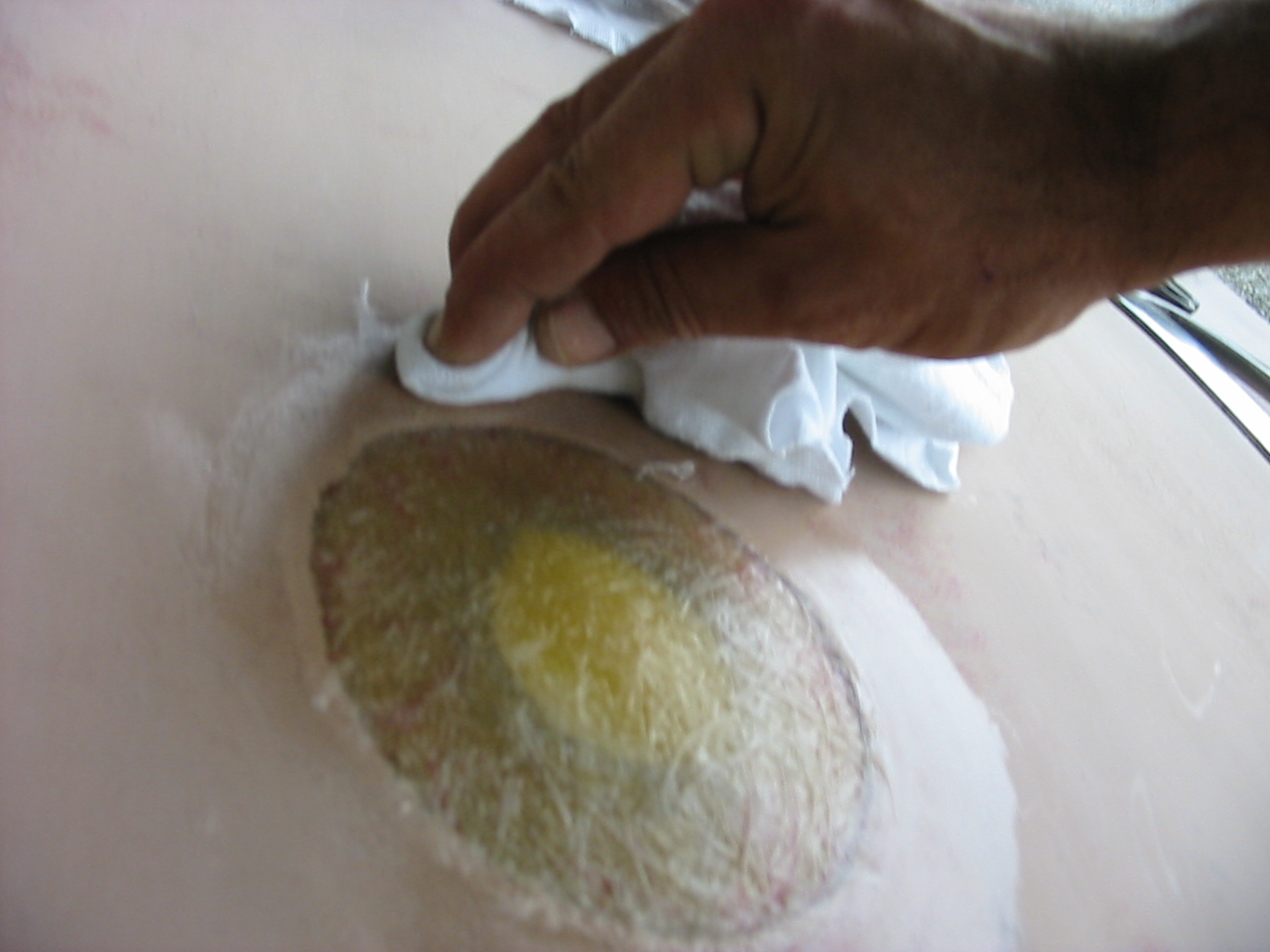
23. Once the fiberglass has kicked, cover surface imperfections with fairing filler
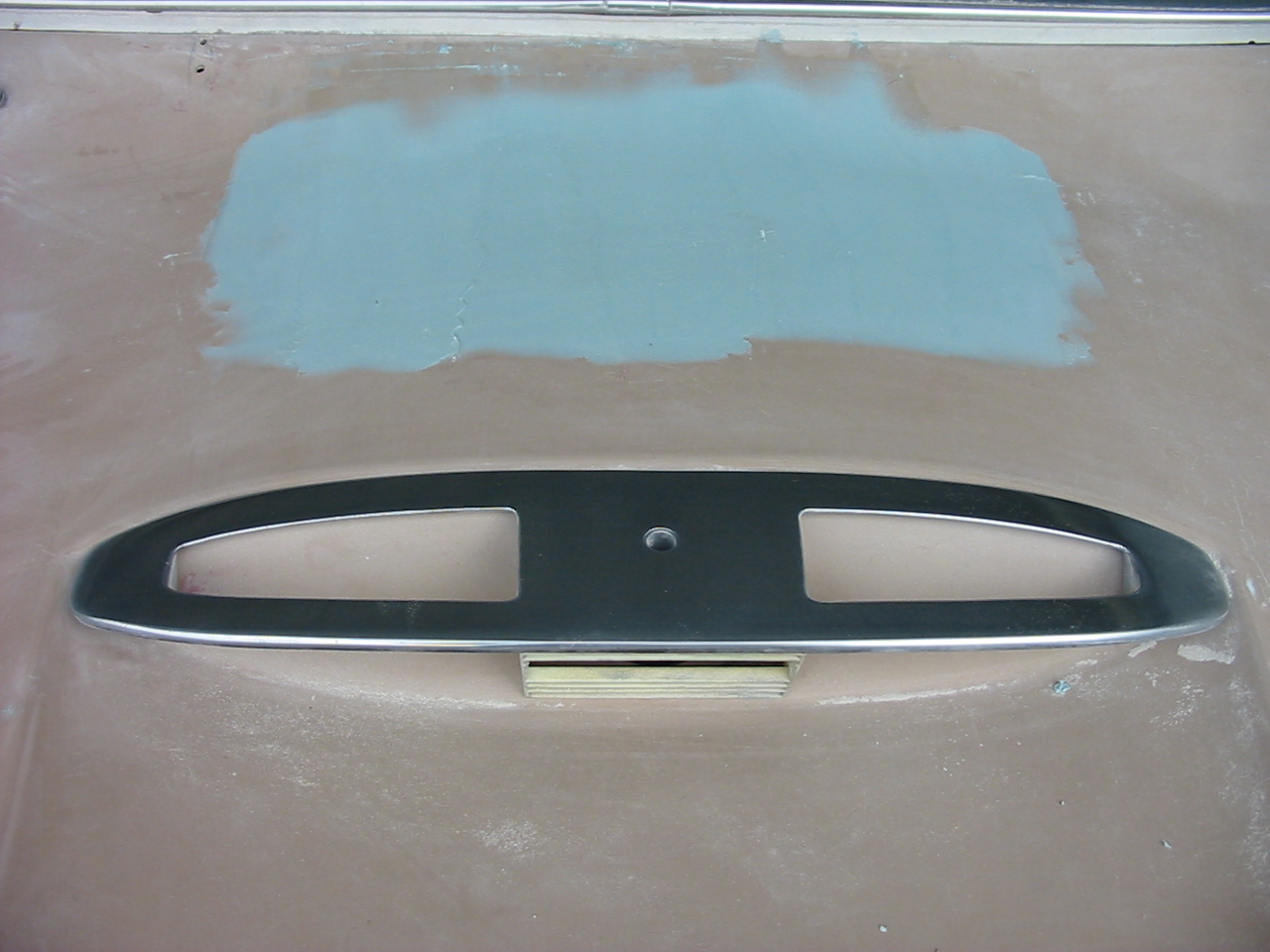
24. Sand it flush and fair. Voila! No more hole.
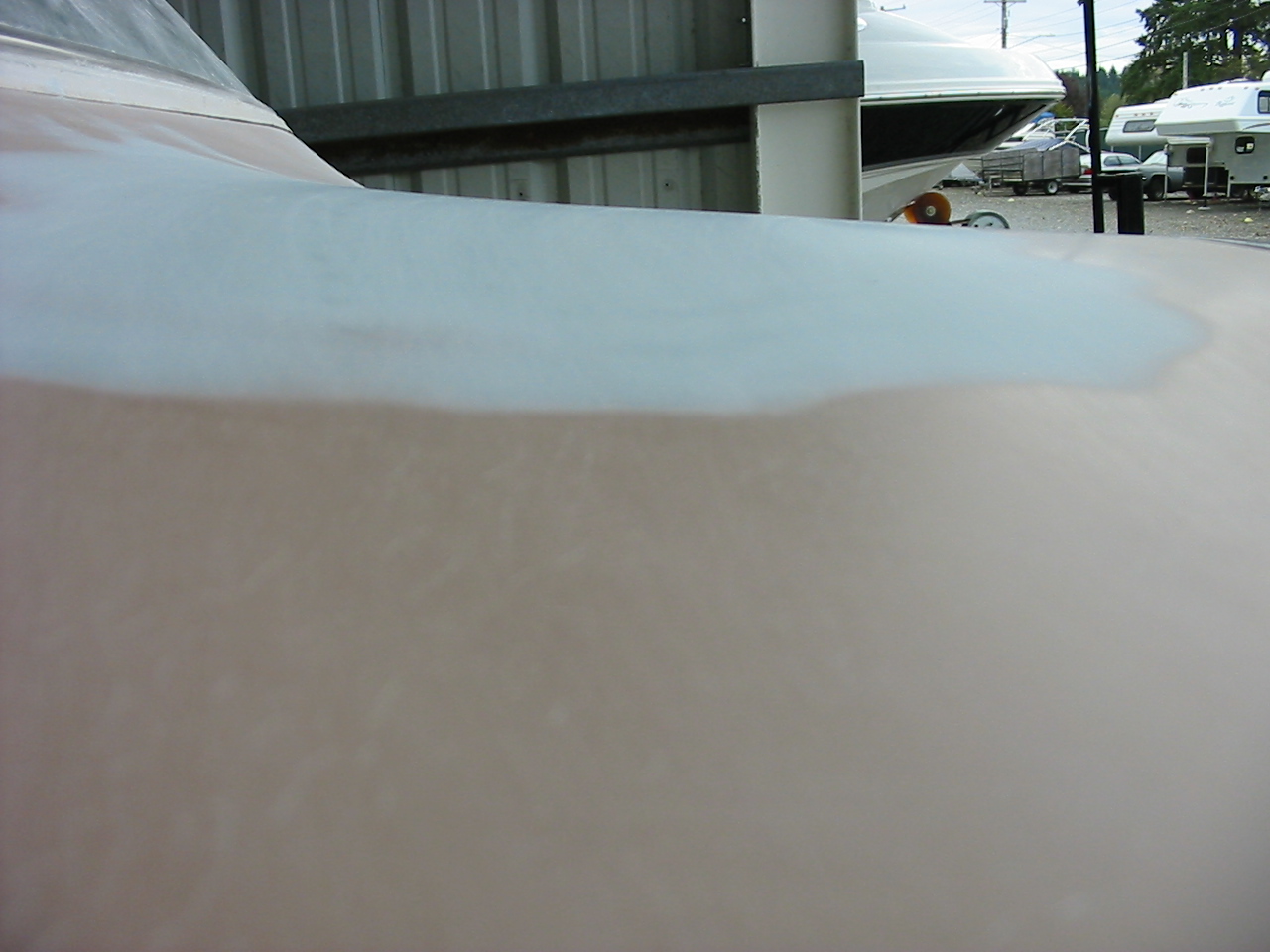
Discuss this article
Log in to comment